Chipped Glass build-plates – What causes it?
Regular and seasoned FDM printer users have probably experienced the problem of chipped glass. After failed prints and warping this is a problem that can disrupt your workflow and cost you dearly. Chipped glass be caused by a number of variables including material and adhesive choices, and printing conditions. However there is one primary factor that causes glass build-plates to break and it all has to do with thermal contraction.
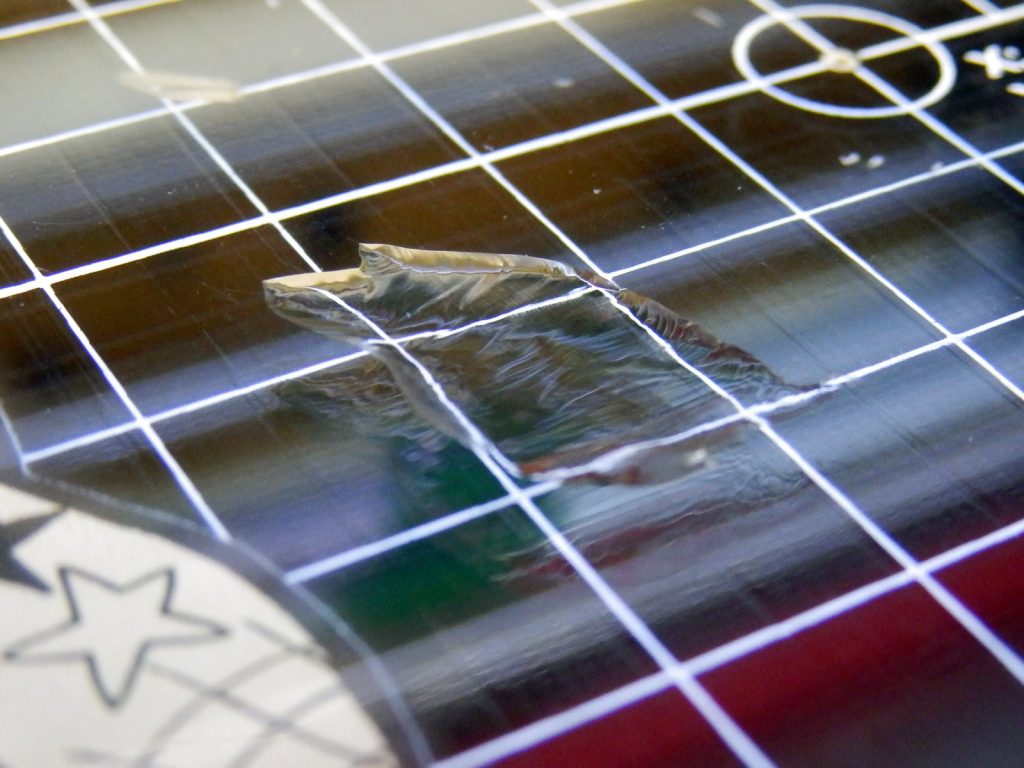
Thermal Shrinkage and Chipped Glass
Most materials expand on heating and shrink on cooling. However not every material shrinks by the same amount on cooling for a constant temperature drop. This property is measured by the coefficient of thermal expansion (CTE). The CTE describes the rate of shrinkage per unit temperature. Glass has a linear CTE of around 1-17 x 10-6 K while that of 3D printing thermoplastics lies in the range of 40 to 200 x 10-6 K. The linear CTE of glass is thus about an order of magnitude lower than that of the printed thermoplastic. As parts cool, a tensile force is exerted on the surface of the glass while the parts are still adhered to the glass. If the parts are adhered too strongly to the build-plate they will continue to exert a tensile force as they cool down further (figure 1a, b).
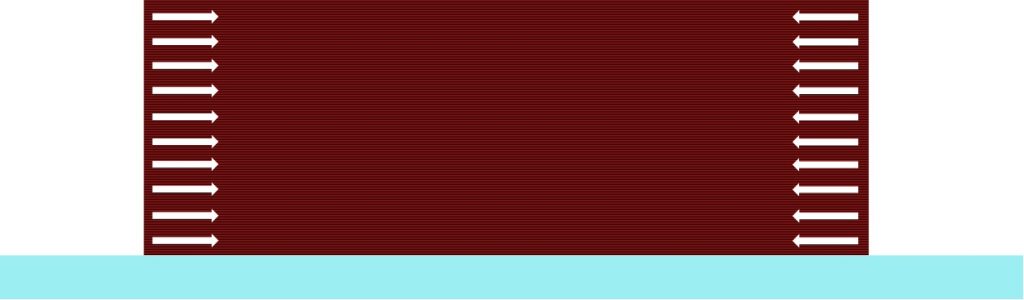
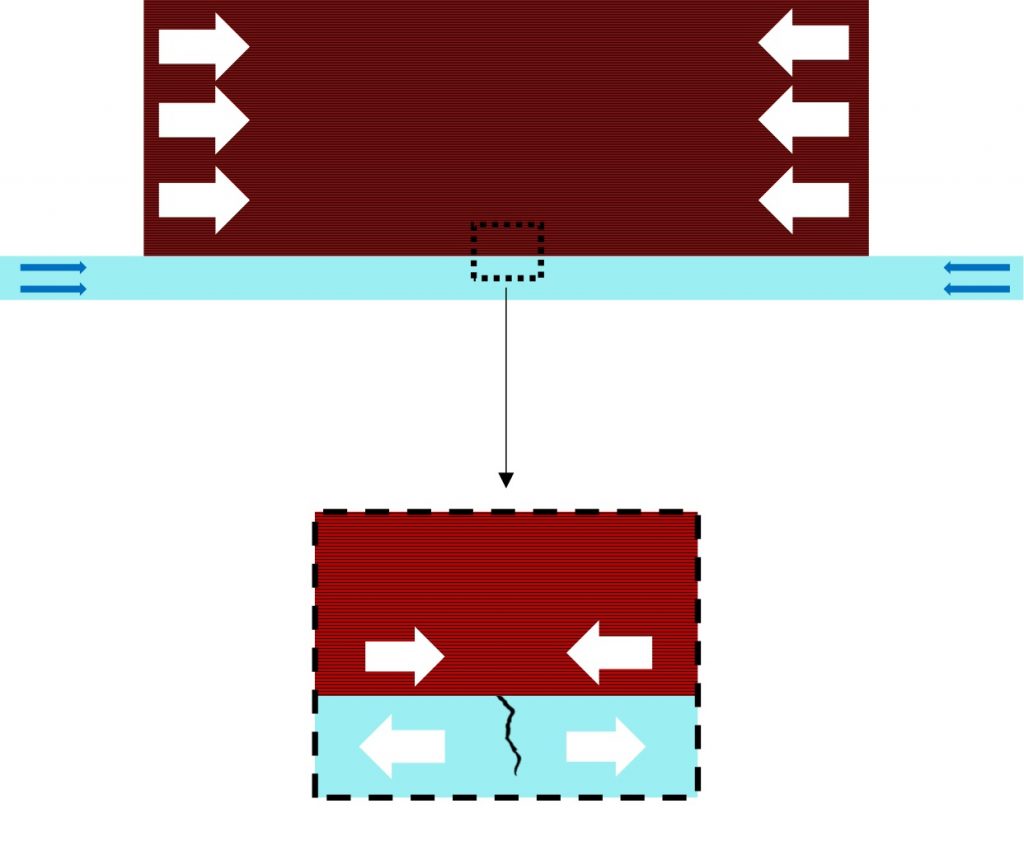
To the naked eye a sheet of glass appears to have a perfect and smooth surface. However at the microscopic level glass has defects. These defect scan either result during the manufacturing process, or else can be introduced during use in the form of scratches. These can act as points of stress concentration and thus increase the likelihood of microscopic cracks to form. Since glass is a brittle material, tensile forces exerted on the surface will cause the cracks to propagate, eventually leading to failure. This can either lead to small piece of glass chipping off the build plate or to a catastrophic failure of the whole glass sheet in some cases.
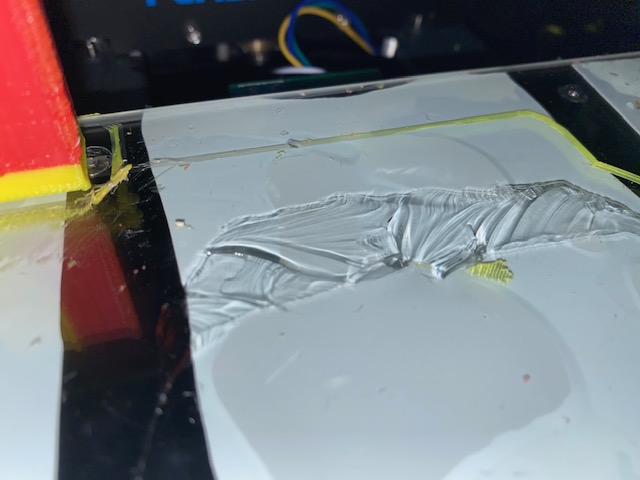
Thus the combined action of thermal shrinkage and the adhesion of the part to the glass can cause enough force to damage the glass surface. Generally this is not a problem, especially with consumer grade filaments and non-demanding printing conditions. Nonetheless several factors can increase the probability of chipped glass.
What makes glass prone to chipping?
Materials
Most users experience problems with chipped glass on switching to PET-G after working ‘chip free’ with PLA. Unlike PLA, PET-G sticks aggressively to glass, and also PEI, increasing the chance that the build-plate will be damaged. As with PET-G some materials can be more prone to danging glass build-plates due to over adhesion.
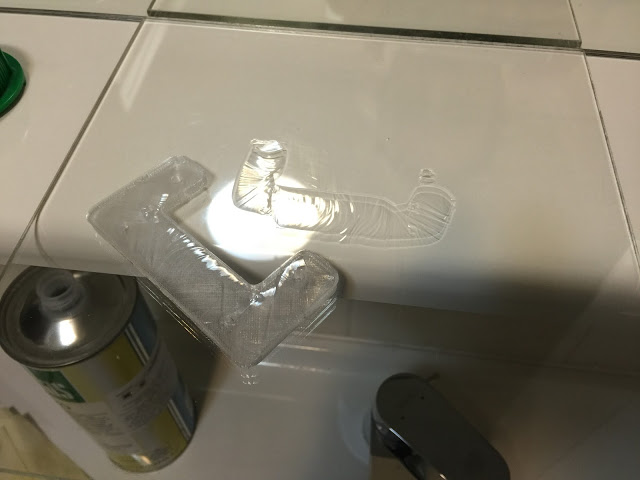
These include:
- PET/PET-G/CPE, PET type materials are very stiff and tend to stick too well to glass and other surfaces in a similar fashion to PET-G.
- Polycarbonate, PC is a very strong and stiff material. While sometimes it has difficulties adhering to glass, the high strength of the material can pull on the glass with so much force to chip or completely crack it.
- ABS, our experience with ABS is generally positive, however some brands of (possibly modified) ABS materials tend to stick too well the the build-plate. This makes the part removal process more difficult and can lead to glass chipping.
- High temperature materials, HT materials such as PEEK require very high build-plate temperatures. Additionally these materials tend to be quite stiff. Thus the high temperature drop combined with the high stiffness of these materials can be a recipe for making glass chips.
- Modified filaments, some filaments such as PLA, Nylon and ABS are modified to improve print-ability and reduce warping. This can cause these types of filaments to over-adhere.
Printing conditions relating to chipped glass
Glass cracking can also be result from the printing conditions which can promote over adhesion or accelerate wear on the glass build plate. These include:
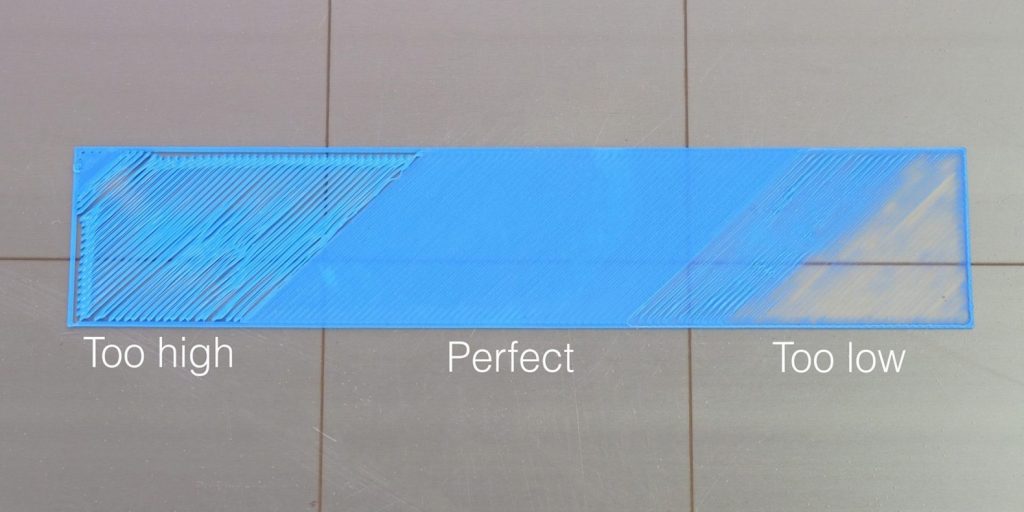
- Printing too close to the build-plate: Printing too close to the build plate will increase the chance that the filament over-adheres to the build surface. Furthermore it can also directly damage the build-surface or increase the rate of wear on the build-plate.
- Over-extruding the first layer: while slightly over extruding the first layer can help with initial layer adhesion, overdoing it can lead to similar consequences as printing with the nozzle too close to the build-plate.
- Removing the part early or cooling the build-plate quickly: Printed parts tend to self-release on cooling. Especially when using a specialty build-plate adhesive (such as Magigoo) . With most materials (but not all) it is advisable to wait for the part to cool completely before attempting removal. Attempting to remove the part while it is still hot can cause unnecessary strain on your build surface. This can lead to premature failure. Similarly cooling the build plate too quickly by taking it out of the printer and putting it on a cold conductive surface can also cause thermal shock and damage the glass sheet.
- Using the incorrect adhesive: Nowadays there are a number of adhesion solutions you can use. Some of them (including our range) are specific to certain types of materials. Using the incorrect adhesive for your materials can cause the part to over-adhere which can damage your build-plate. Our adhesives are carefully formulated to provide the right amount of adhesion according to the material. Furthermore Magigoo adhesives ensure that part removal is as easy as possible.
- Using too much adhesive: Using too much adhesive can also lead the part to over-adhere to the build-plate.
Wear and tear
With every print, the surface of glass (and other materials) will deteriorate. Every heating and cooling cycle and part removed will introduce further defects and exacerbate existing ones. This is inevitable and some materials as mentioned above will wear the surface more quickly.
The wear on glass build surface can also be worsened when using sharp tipped tools to remove parts. These might introduce scratches to the surface of the glass which can act as points of stress concentration and eventually leading to cracks and chips.

Join us in the next post to see how you can reduce the chances of damaging your build-plate by modifying slicer settings and printing conditions. Until then happy and safe pritning!