Prevent warping – Temperature and first layer adhesion
Our chemist, Jean Paul Formosa, discusses how one can prevent warping in 3D printing by investigating its causes. This is part two of a four part series. Check out part one here.
Preventing warping
The solution to prevent warping is to ensure that the adhesion between the first layer of the printed object and the build plate is larger than the thermal stresses on the first layer. The warp of a print can be mitigated by controlling build-plate adhesion and the thermal gradient. The first layer adhesion depends on several factors, these include:
- Build-plate material
- Adhesive used
- Type of material being printed
- Build-plate temperature
- Nozzle temperature
- First layer print speed
- First layer flow
- Good build-plate levelling
The first layer adhesion is generally stronger when the bed temperature, nozzle temperature and first layer flow are high and the first layer print speed is low. These settings however, are highly dependent on the printer, material and environment combination.
Prevent warping by controlling the thermal gradient
A good control of the thermal gradient during FDM printing can also help in reducing warp by reducing thermal stresses. This is generally, but not necessarily achieved by keeping the internal build temperature slightly (10 ° – 20°C) lower than the glass transition temperature of the material being printed. The glass transition temperature is the temperature, or rather a temperature range above which a thermoplastic material starts acting like a rubber. Below the glass transition temperature the material is in a hard ‘glassy’ state. In layman’s terms below the glass temperature the material is hard and strong while above this temperature the material is softer and less stiff. This means that close to the glass temperatures the thermoplastic exhibits lower thermal stresses since it is softer.
For a large portion of FDM filament materials, the temperature inside a printer without an actively heated and enclosed chamber is not enough to be close to the glass point of the material. Nonetheless keeping the build temperature constant is key to prevent printing issues. It is always advisable to prevent any drafts and sudden changes in temperature when printing.
Some engineering materials such as Nylon and ABS can be easily printed in enclosed printers with heated beds. The heated bed would be sufficient to keep the internal temperature of the printer high enough to mitigate warp, if a strong enough build-plate adhesive is used. On the other hand high temperature materials such as virgin PC, PEEK, Ultem and PPSU will probably require a heated chamber in order to reduce the thermal stresses during printing which often leads to warping and other artifacts. Other factors which may affect thermal stresses include, layer height, print speed, shell thickness and infill percentage, with higher values generally leading to a higher tendency to warp.
Build temperature and its consequences
Looking at this information above one might think that just increasing the build plate temperature as much as possible will prevent warping. Unfortunately this is not the case with most FDM materials. Increasing the build-plate temperature too much can cause three major issues:
1. The most obvious issue is a loss in print quality due to the printed polymer on the build-plate being too soft. This will usually cause curling at sharp edges and leads to deformation of the part (Figure 1).
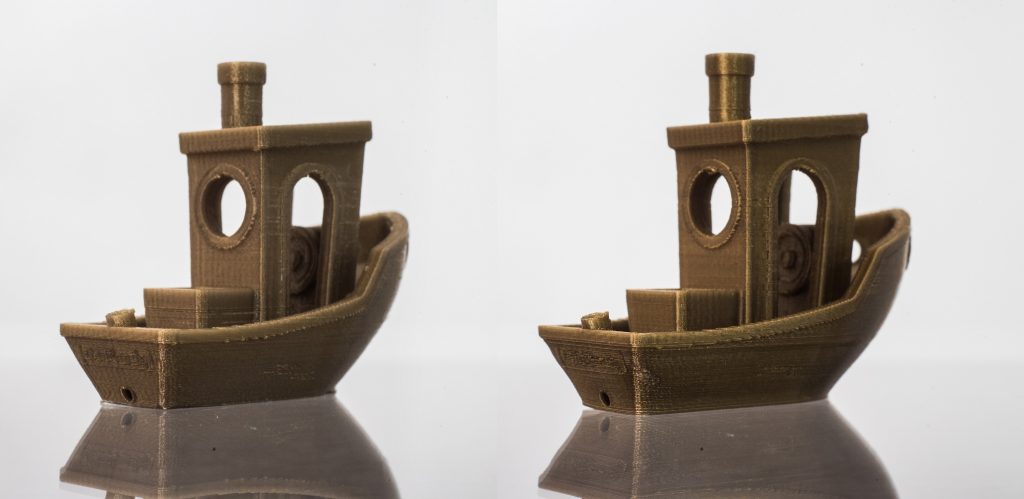
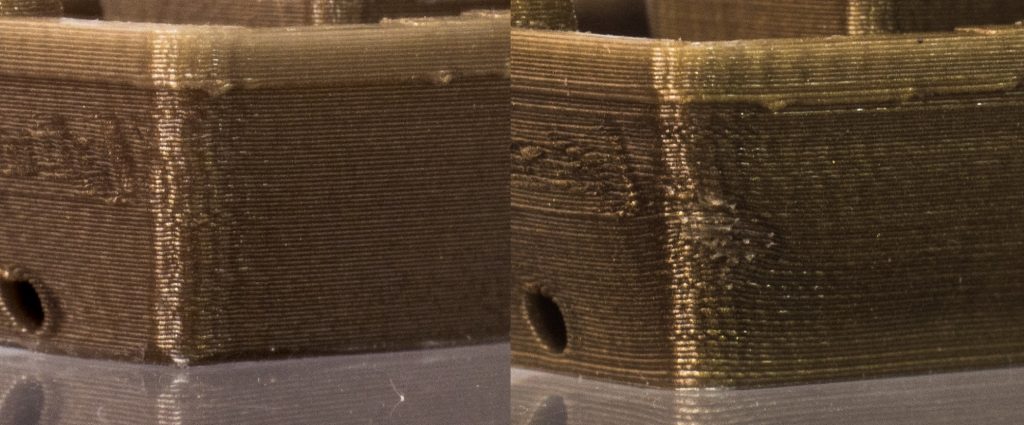
2. As the print height starts increasing, the mass of material at the bottom of the print i.e. the first few millimetres or centimetres, need to be stiff enough to stop the thermal stresses from the newly deposited layers of the print to stop influencing the base of the print thereby arresting any further warp (Figure 2). If the temperature of the build-plate is too high, generally, the base of the print will be soft enough to allow the additional layers on top of the print to pull on the base of the print.
A practical example is when comparing the behaviour of rigid printing materials to that of flexible materials. Rigid materials such as ABS or PC usually do not continue to warp, or warp significantly less as the print reaches a certain height. On the other, hand flexible materials such as PP or nylon will keep on warping significantly as the print progresses and reaches its full height. That is, if the build plate adhesion is not strong enough.
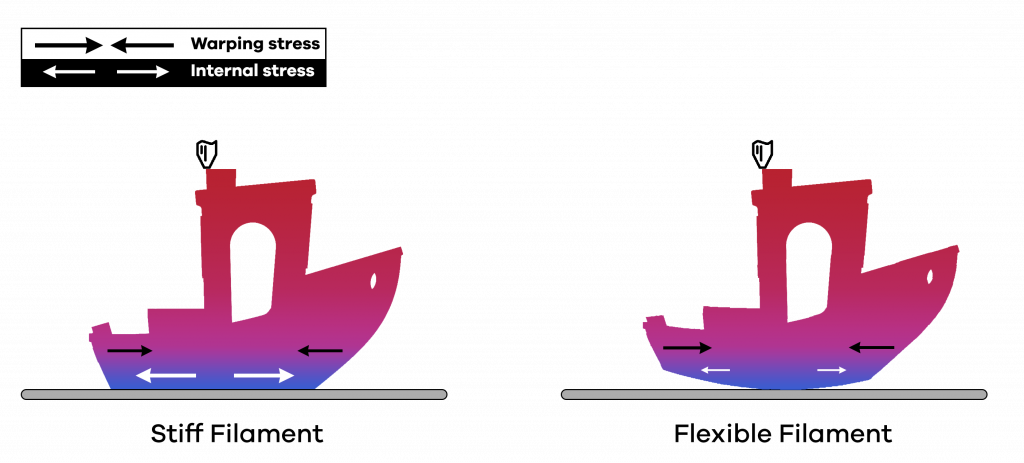
3. Another factor is related to the nature of the adhesive. While at higher temperatures the adhesion between the plastic and the adhesive is usually greater, the actual strength of the adhesive layer will start decreasing. Most adhesives, and even build-plate surfaces are made of polymers which soften as the temperature is increased. As a result, there will exist a range of temperatures for each material in which the warp of the part being printed is at a minimum. In this range there will be a compromise in which the first layer adhesion is maximised. The adhesive layer strength is also maximised and the thermal and warping stresses are minimised. For some materials this optimum range might be wide. Nonetheless, for most high performance materials the optimum printing temperature range can be as small as 5-10 °C.
For these reasons determining the best printing temperature in your 3D printing system is important for preventing warping with Magigoo® adhesives.
In part three we will discuss in further detail how to determine this optimum printing temperature range and share with you some tools and tips to make this an easier process. So, stay tuned and happy 3D printing 🙂