Owens Corning and Thought3D collaborate to launch adhesive for the XSTRAND composite filament GF30-PP.
Owens Corning and Thought3D collaborate to launch adhesive for the XSTRAND composite filament GF30-PP.
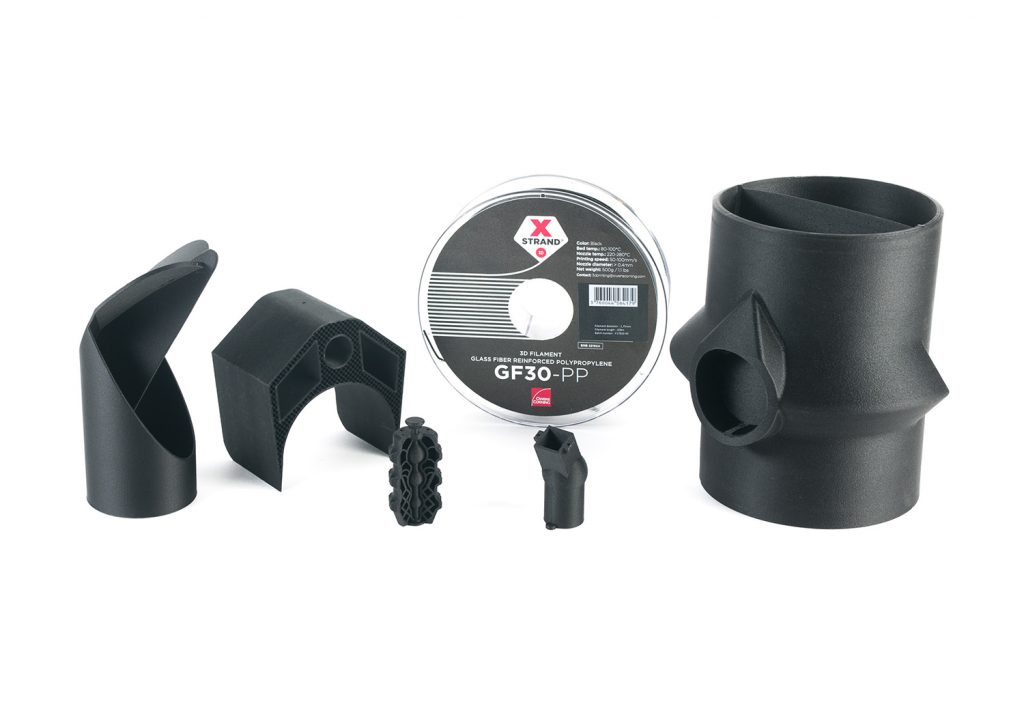
Recently Thought3D launched its line of adhesives for professionals, targeting multiple engineering filaments known to be challenging to print with. Magigoo PP-GF was specifically designed in collaboration with Owens Corning to work with their XSTRAND GF30-PP material and it aids in the first layer adhesion for challenging prints.
XSTRANDTM GF30-PP is an engineering-grade material composed of 30% glass fiber and a polypropylene filament for 3D printing. It is designed to go beyond functional prototyping and meet the demands of the real world. It is used for production of tooling and end use parts aimed for transportation, electronics,appliances and equipment and sports industries.
Chris Skinner, VP of Strategic Marketing in Owens Corning says “We stand together with Thought3D and celebrate their launch of Magigoo. With a shared passion to redefine Advanced Manufacturing and 3D-Printing Solutions for Industrial Markets, we are thrilled to now enable larger, more functional parts and component printing with increased surfaces and minimum warping – all built with the structural integrity, toughness and durability that only Owens Corning’s XSTRANDTM GF30-PP 3D-printing filament can offer. The future is bright and solutions like Magigoo make the pursuit of what’s currently considering impossible a bit more realistic.”
Co-Founder of Thought3D Andrei-Andy Linnas says “It was a particularly interesting challenge to come up with a specialty adhesive for this material as it is well known that it is difficult to adhere polyolefin materials to other types of materials. Introducing glass fibres in the material required a completely new adhesion technology and formulation. Our hard-working team did it in a record four months and we are happy with the results. We will work closely with OwensCorning to bring Magigoo PP-GF closer to the end users in coming months. We are sure it will improve the printing performance of this really functional and strong material.”.
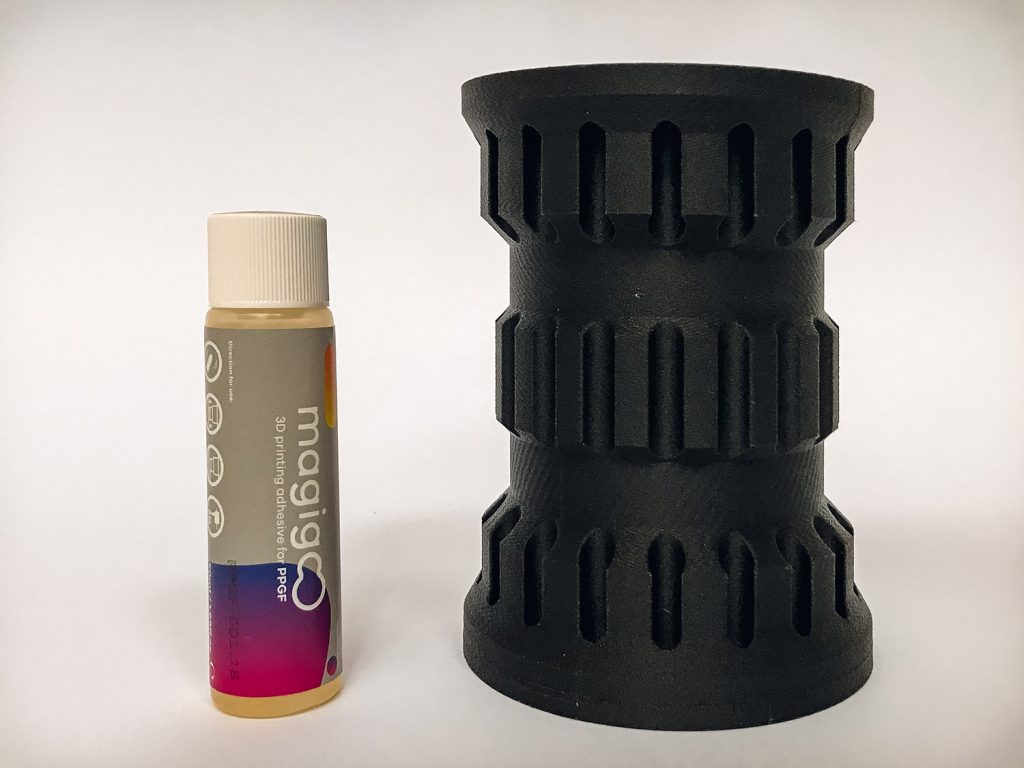
About Owens Corning and XSTRAND TM:
With over 19,000 employees worldwide, Owens Corning, a world leader infiberglass composite materials, roofing, and insulation industries has 3D printinglabs in Ohio, US and Chambéry, France. Earlier this year Owens Corning launchedits 3D printable XSTRAND TM branded line of composite materials.
The need for a new material came from within. At Owens Corning, one of the company’s biggest challenges was in creating its own custom tools and fixturesfor use within the company. With long lead times from external manufacturers and high costs, the need for a new solution was apparent. Even when parts do arrive quickly, often they were not fit for purpose, so they need to be reiterated,quickly and cost-effectively.
For example, in the roofing division of the company, they needed a customized guard replacement that was not available off-the-shelf. Rather than turning to their manufacturers, the company looked Internally to their 3D printing lab for a solution. The guard protects a sensitive component from any flying debris in avery hot, high-speed, and tough production environment. It required strength,chemical resistance, and temperature resistance. Building on Owens Corning knowledge of fiber glass and combining it with engineering filaments resulted in stronger, tougher XSTRANDTM materials. Now using 3D printing, the company was able to produce and iterate the part at a fraction of the cost and time that it would have taken if outsourced. The company currently uses 3D printing to solve many of its own in-house needs. Last year, it recorded over 17,000 hours of print time, with printers typically running 24/7.
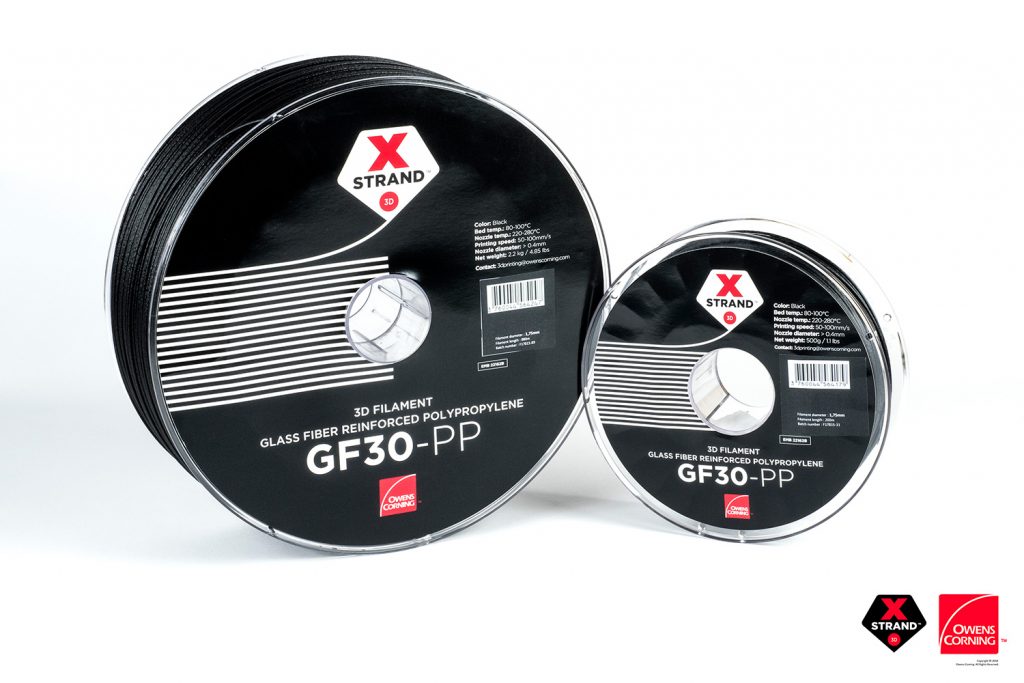
About the adhesive and challenge:
Polypropylene (PP) is a thermoplastic semi-crystalline polymer exhibiting properties of good strength, impact resistance and ductility making it useful as an engineering material. PP however is a soft material and like most plastics it can be strengthened by the introduction of fibres to make a polymer composite material such as GF-30PP. These materials are usually stiffer and stronger than the parent polymer and can result in a material with a very high strength to weight ratio. This type of material required a completely new adhesive formulation to play to its distinctive characters.
Dr Keith M. Azzopardi and Jean Paul Formosa, chemists behind formulation of new adhesive commented “Even though GF30-PP can be expected to lesser extent of warping and glass fibres aid with the adhesion to glass bed it is still likely that medium and large print objects can warp to higher extent, because materials’ higher stiffness may be overcoming the expected advantages of glass reinforced PP. We designed this adhesive from scratch in just four months constantly iterating and finally resulting in one that is tuned to provide strongest adhesion without breaking hardware, easy release and easy cleaning experience.“
About Thought3D – Thought3D is a R&D startup based in Malta. In 2014 the company experienced the first layer adhesion problem first hand and came up with a novel smart adhesive, that sticks when hot and releases when cold. Today, Thought3D produces and sells Magigoo worldwide through a network of resellers and industry partners. Thought3D aims to provide superior user experience in 3D printing by solving the adhesion problem of engineering plastics. Company has released its smart adhesives for professionals for Polypropylene and Polycarbonate filaments and planes to release adhesive for Nylon filaments in the near future.
