3D Printing Tips – Fused Deposition Modelling (FDM)
Following our latest blog post all about what Magigoo is and why it’s useful for the FDM process, this blog post will provide readers with some general tips for 3D printing. These tips and rules of thumb will maximise the print quality and longevity of your 3D printer.
3D Printing Tip #1 Clean your build plate for optimal results
If you’re having trouble with first layer adhesion, this tip may help. Clean your build-plate of any debris or adhesives. Avoid using detergents to clean your build-plate, as the residues of these products can interfere with adhesion. You can clean your build-plate with water and a microfibre towel. However, if the water is not sufficient due to the presence of oil or grease, you can use ethanol or Isopropanol.
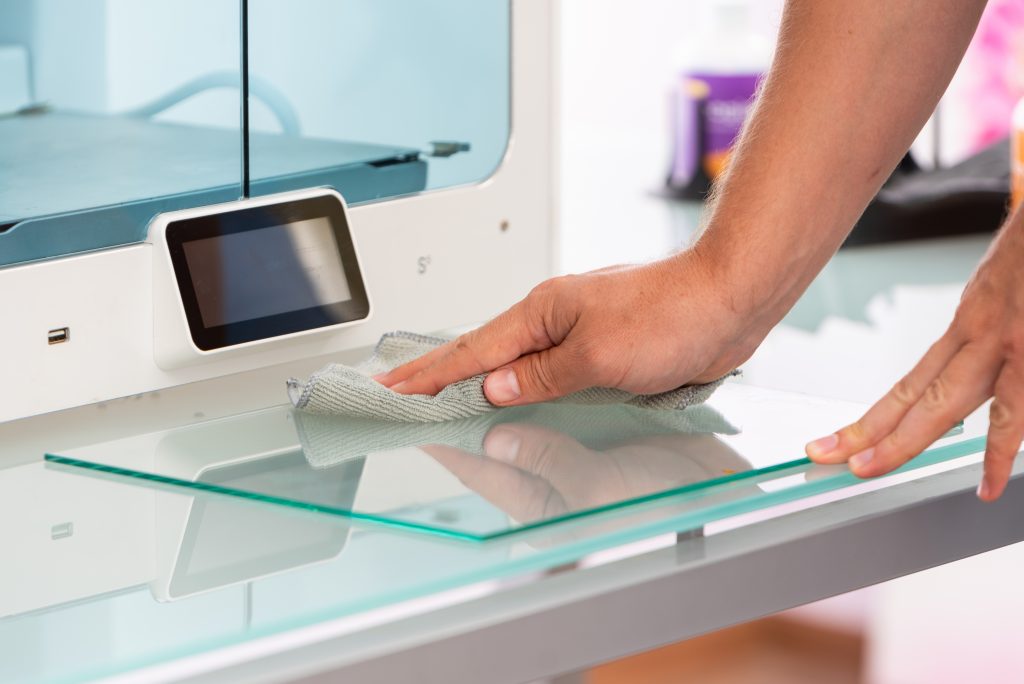
3D Printing Tip #2 Purge the nozzle when loading a new filament
Whether you are changing, loading or unloading filament it is always a good idea to purge. Purging involves feeding the filament through the extruder to clean out the nozzle internally. When changing or loading a filament, purging for a couple of minutes ensures that remnants of the previous filament are completely removed from the nozzle. When it comes to unloading filament, purging the filament for a few seconds decreases the chances of the filament jamming in the hot-end!
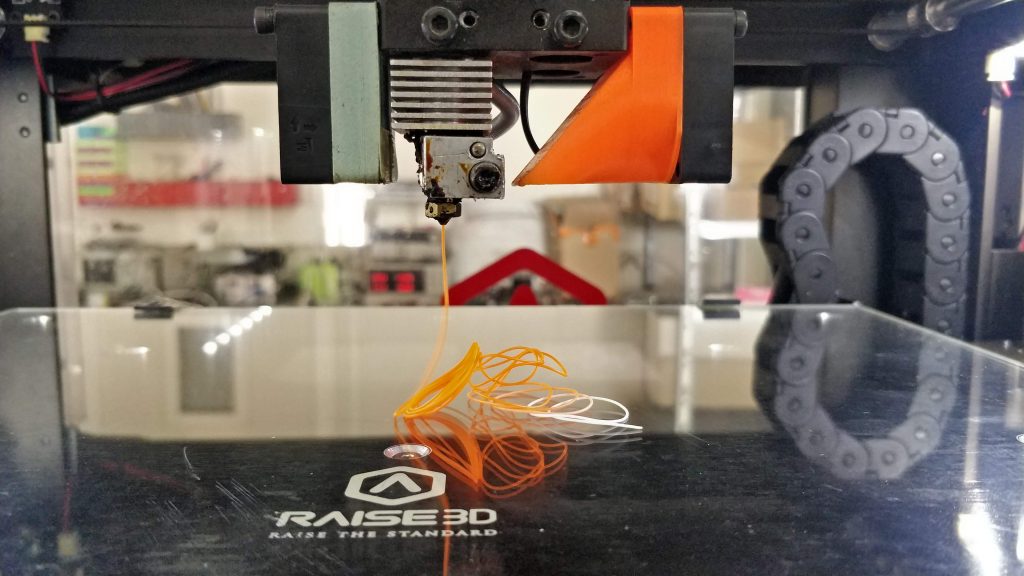
3D Printing Tip #3 Determine the optimal build-plate temperature for your material
This process of finding the best build-plate temperature for 3D printing is relatively simple but often overlooked. It consists of testing different build-plate temperatures with a simple warping test print for a given material/adhesive combination on your printer. This will help you find the temperature at which your prints are least likely to warp! Finding the optimal build-plate temperature for the material ensures that your prints come out with the least amount of warp possible. You can read more about this in our Magigoo Manual!
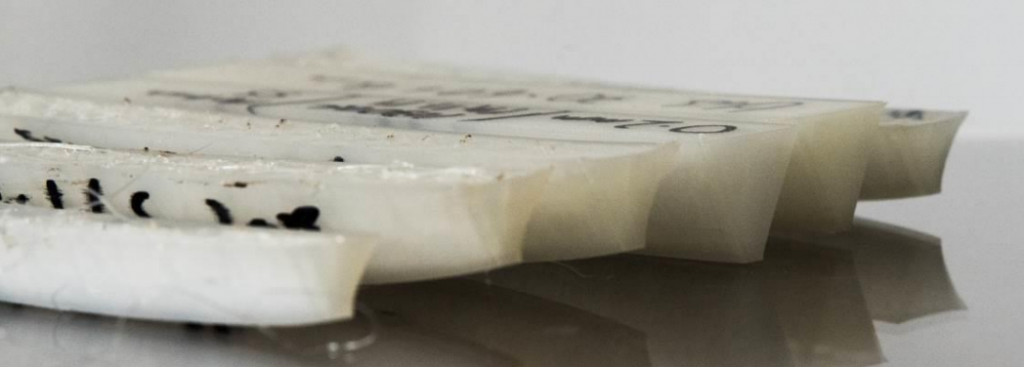
3D Printing Tip #4 Maintain and calibrate your 3D printer
If you own a 3D printer and have never done maintenance on it, you might want to take a special note of this tip. Whether you 3D print mechanical parts or small hobby models, it’s a good idea to consider doing some maintenance on your 3D printers.
It is recommended that you perform maintenance tasks every one to three months depending on the frequency of use of the printing. The following are some of the standard maintenance tasks that we perform on our 3D printers:
- Clean the printer and remove debris.
- Clean build surface thoroughly using warm soapy water, followed by isopropanol. PEI surfaces can be treated with fine-grit sandpaper to restore adhesive properties.
- Check the tension of belts and adjust if necessary. Also check for any play or dead spots in the hot end carriage.
- Clean and re-lube guide rods/rails with light machine oil.
- Clean and re-grease lead screws with synthetic grease.
- Clear the nozzle from debris.
- Perform a nozzle cleaning procedure.
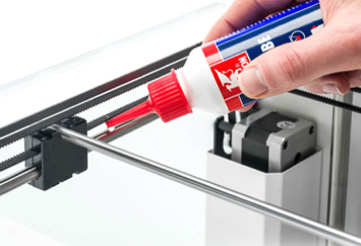
3D Printing Tip #5 Use the Preview feature in your slicer before printing
It’s recommended to always check the preview of a print when slicing your 3D models. This is a powerful tool which can help you identify any potential printing issues before printing starts. Most slicers have the possibility to detect the presence of overhangs and thus the need for support placement. This will allow you to check if certain parts of a model were left unsupported. Furthermore, the use of the preview can also highlight any mesh errors in your model which might not be immediately apparent before slicing. These include non-manifold edges and disconnected bodies which can either result in unsuccessful prints or weak parts!
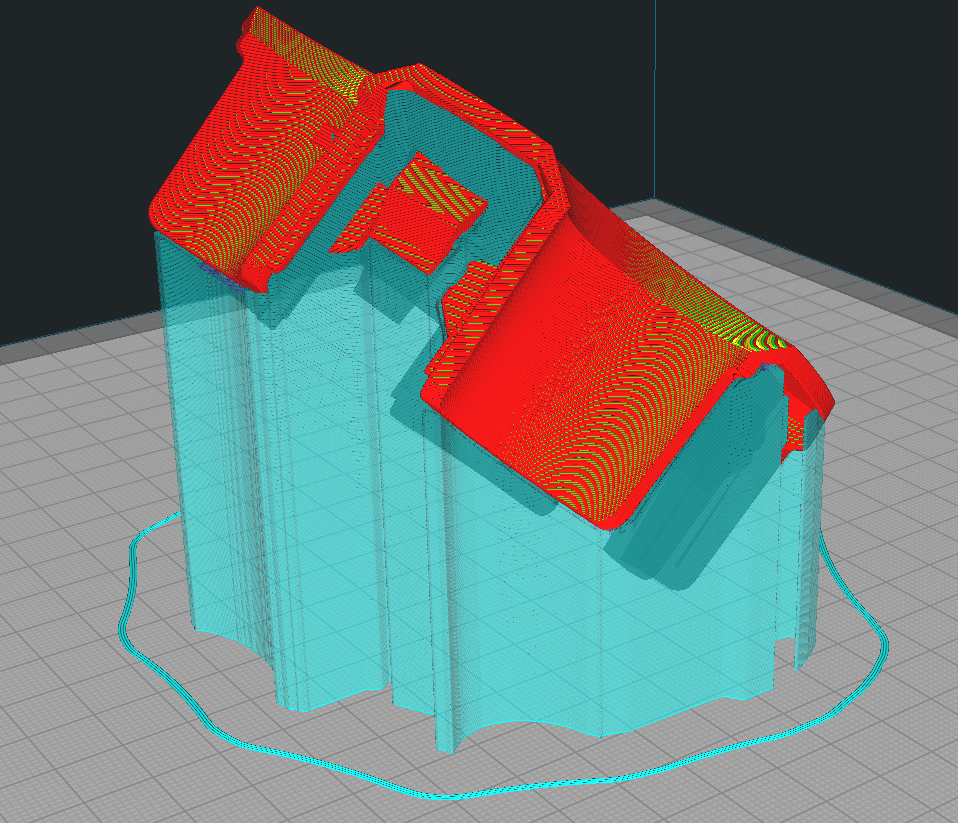
3D Printing Tip #6 Design and print with tolerances in mind
A useful tip when it comes to 3D printing and designing a part is to print and design considering tolerances. Different 3D printers have different tolerances which can be accounted for during slicing. Several modules exist online to help you fine-tune your machine to more accurately reproduce part dimensions. Nonetheless, it is still a good idea to allow for some room for tolerance when designing 3D printed parts to ensure that printed parts can fit over each other. A general rule of thumb is to allow for about 0.1-0.15 mm of tolerance when designing parts that fit into each other. This should prevent issues where the parts don’t fit into each other due to errors such as holes being printed too small.
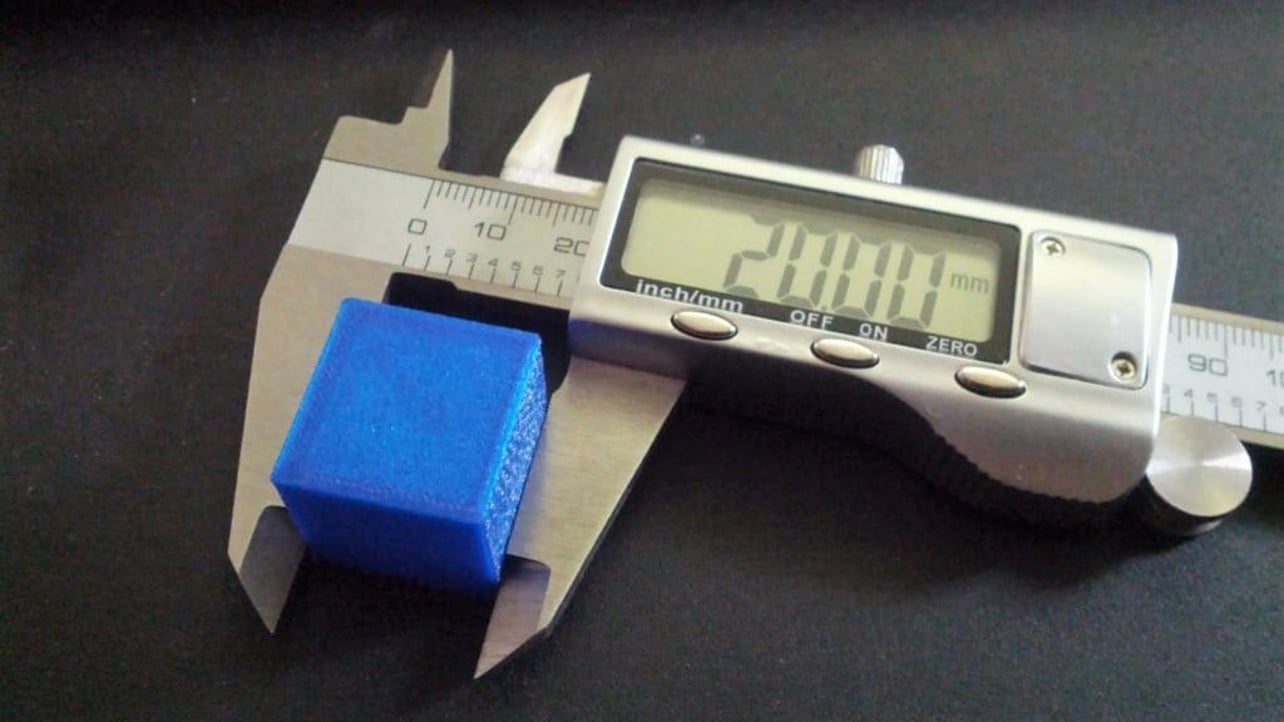
3D Printing Tip #7 Removing a print that is stuck to the build-plate
Magigoo adhesives are designed to make part removal easier after printing. In fact, most materials pop off the build-plate after it cools down. Some materials such as flexible materials, however, might not show this behaviour due to their flexibility. For flexible materials which are hard to remove or for delicate parts, we recommend wetting around the build-plate. A few squirts of water should be enough. After waiting for a few minutes the print should be removed with ease.
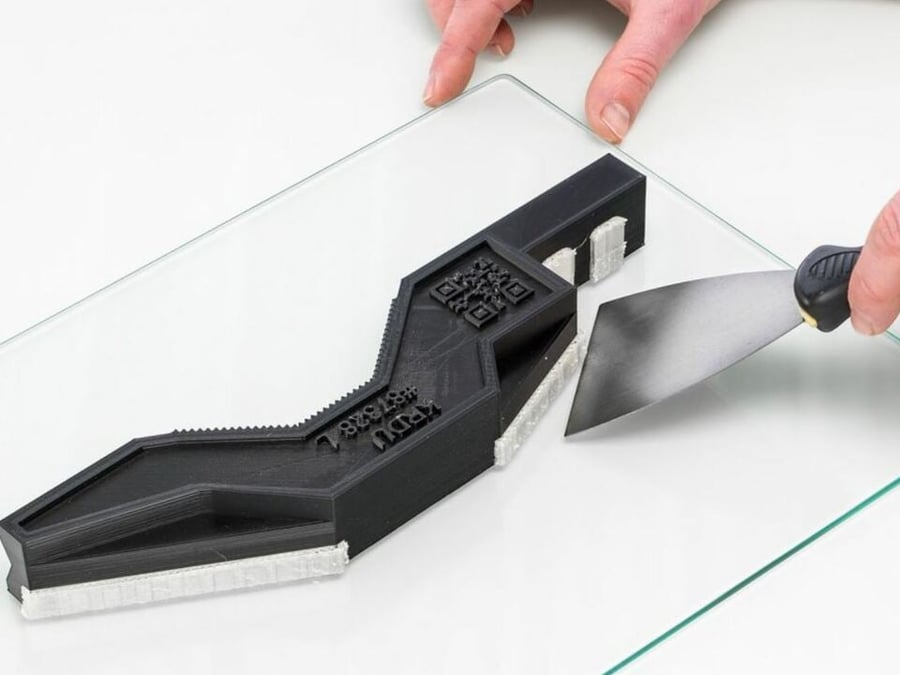
3D Printing Tip #8 Pritning stronger parts
We routinely print some functional parts for our production line and other projects. This requires that the parts are as strong as possible. Apart from printing the part in a suitable orientation and material, you can also tweak your slicer settings for improved part strength. Here are some parameters which can help you achieve a stronger print:
– Increase extrusion width
– Increase the number of perimeters
– Slightly increased nozzle temperature
– Decrease or eliminate part cooling
– Using an enclosed printer or a heated chamber
– Increase nozzle size

3D Printing Tip #9 When unsure, ask for help!
This 3D printing tip is probably the most valuable one! 3D printing can sometimes be frustrating especially when facing unexpected problems! Fortunately, the 3D printing community is full of other makers who are more than happy to assist you with your 3D printing issues. and share their experience on online 3D printing forums.
Feel free to contact us at feedback@magigoo.com or check out our Help Page if you have any feedback or require some advice. We love to hear from you!