3D Printing PP (Polypropylene) – Why and how?
Following last week’s blog article about Polycarbonate, this week we will be looking at another interesting FDM printing material. Polypropylene can be regarded as the opposite of Polycarbonate. While PC is strong and stiff, PP is relatively soft and easily deform-able. This week we shall take a look at the properties and the challenges faced when 3D printing PP (Polypropylene)
What is PP?
PP is a very useful material and is one of the most commonly used thermoplastics in injection moulding due to its low cost and flexibility. PP has a relatively simple chemical structure and is very similar to polyethylene both in chemical structure and mechanical properties. PP can also be co-polymerised with PE to further optimise its mechanical properties.
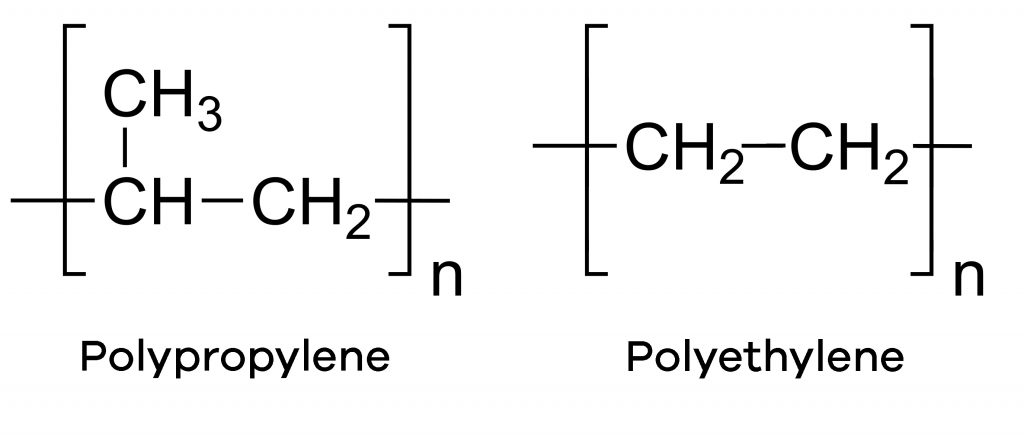
Some of the properties of PP are:
- High toughness
- Can be used in food safe applications, since it does not leach chemicals
- Resistant to attack by acids, water, detergents, oils and fats
- Soft and flexible
- Resistant to fatigue i.e. less prone to failure under repeated loads
- Some grades can show surprisingly good heat resistance
This means that PP finds its way in a variety of products including food packaging, food containers, utensils, athletic apparel and automotive parts such as car batteries. PP utensils can also be autoclaved and thus PP also finds use in laboratory and surgical equipment. Due to its fatigue resistance polypropylene is often used for the creation of living hinges.
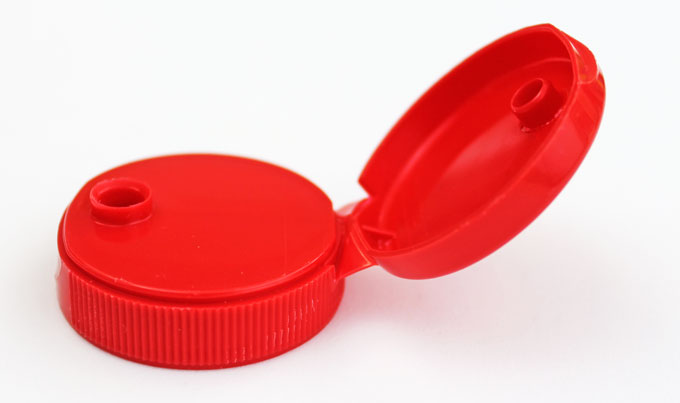
Polypropylene and FDM
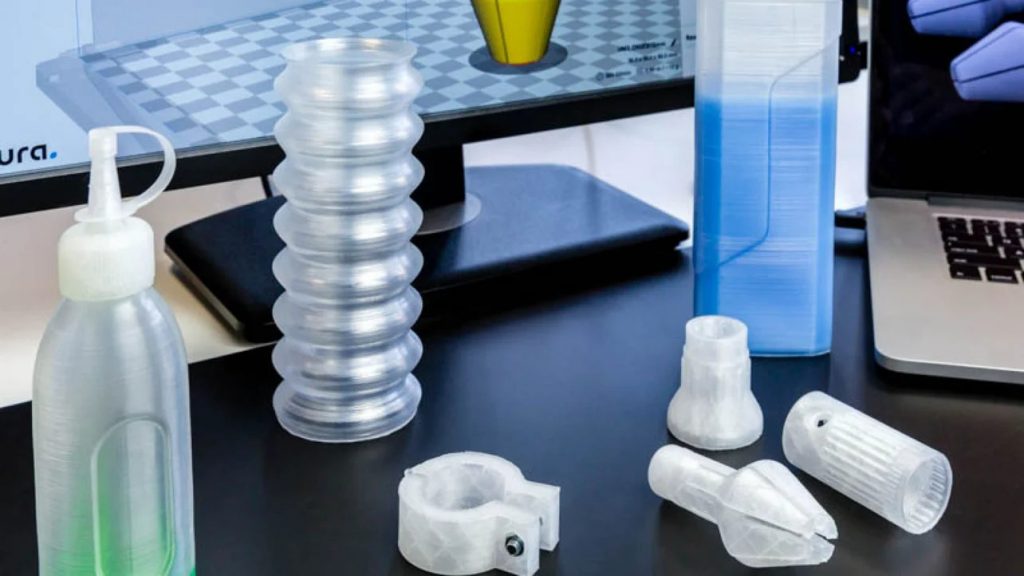
3D printing polypropylene can be challenging
While PP is cheap and widely used, PP is often overlooked as an FDM printing material. Due to its relatively simple non-polar structure PP shows very low adhesion to most surfaces. Furthermore its simple structure also means that polymer molecules can easily pack near each other making it more prone to crystallisation. Thus PP and PE materials can shrink considerably on solidification. As a result of both of these inherent properties, PP and PE parts can warp significantly on cooling. Furthermore these materials have a glass transition temperature which is usually below room temperature. As a result these materials will slowly solidify during printing and after printing leading to more pronounced levels of warp in prints.
Other drawbacks encountered when printing PP include:
- Filament can be hard to print with some extruder set-ups: The inherent flexibility of the material means that most Bowden extruders and some direct drive extruders can have difficulties pushing this material to the nozzle. Furthermore this material is prone to jamming when retraction is used. As a result this material tends to ooze and string.
- Material needs to be printed slowly to avoid jams and ensure good filament flow
- Some filament types require very precise temperature control: Some filaments are very prone to warping and might require additional experimentation with cooling settings for optimal results.
- Support removal is challenging: due to the excellent layer adhesion of this filament it is very hard to remove supports from printed parts. Furthermore this material does not bridge very well.
Advantages of 3D printed PP parts
On the other hand PP can have a number of advantages over other 3D printing materials such as:
- Low moisture absorption: the relative inertness of PP makes it practically impermeable to water
- Low density: PP has one of the lowest densities of any of the currently available FDM thermoplastics
- Excellent layer adhesion: Parts printed in PP tend to have very good layer adhesion and are rarely prone to layer splitting
- Excellent flexibility: PP can be used to make easily deform-able lightweight parts when printed with thin walls and light infill. On the other hand tough parts with exceptional impact resistance can be produced when printing solid parts with thick walls.
- PP usually requires low printing temperatures: Most PP materials can be printed using a nozzle temperature of 200-220 ˚C and a build-plate temperature of 60-80 ˚C.
- Water tight parts can be easily 3D printed: Due to the very good layer adhesion of PP water tight parts can often be easily produced using a few slicer tweaks.
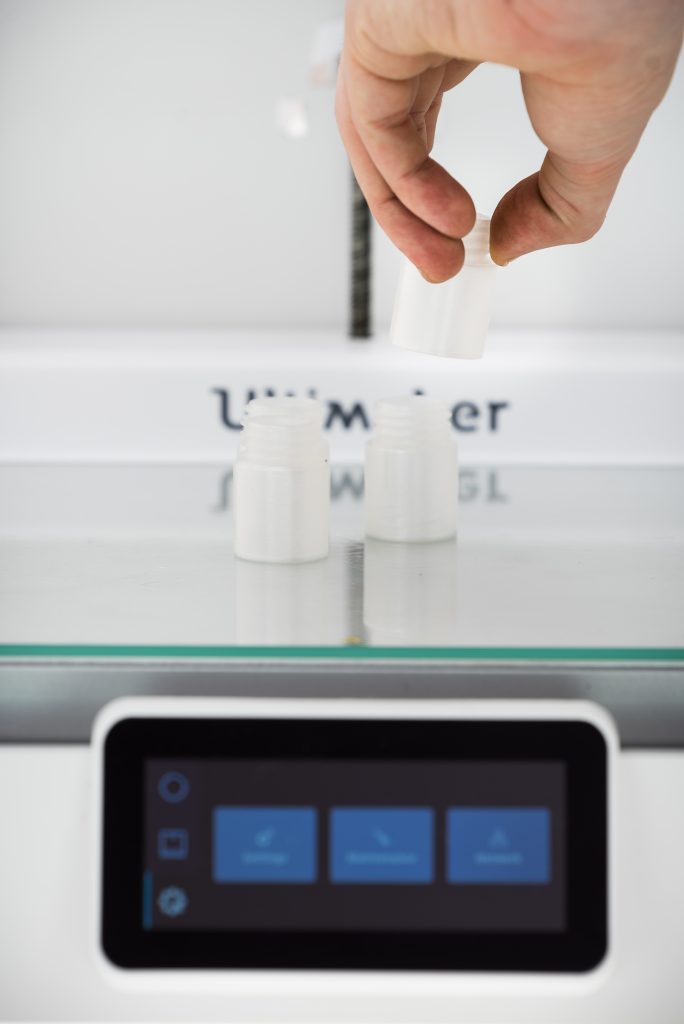
How to succeed when printing PP
Temperature control
With most filaments temperature control is very important, with PP it is even more important due to the effects of crystallisation. Thus apart from determining the optimum build-plate temperature and using an enclosed printer, careful tuning of print cooling might be required.
Crystalline or semi-crystalline materials tend to crystallise to a higher degree when they are cooled slowly. PP might benefit from quick cooling as opposed to slow cooling in regards to shrinkage. Of course one also has to consider the temperature gradient as cooling too quickly can still lead to warping and also poor layer adhesion. In some cases using 20-40% cooling can help reduce the amount of warp. As with most processes this will require some fine tuning and experimentation. We have already tested the optimum settings for some materials on different printers, find out mere here!
Tips for better bed adhesion
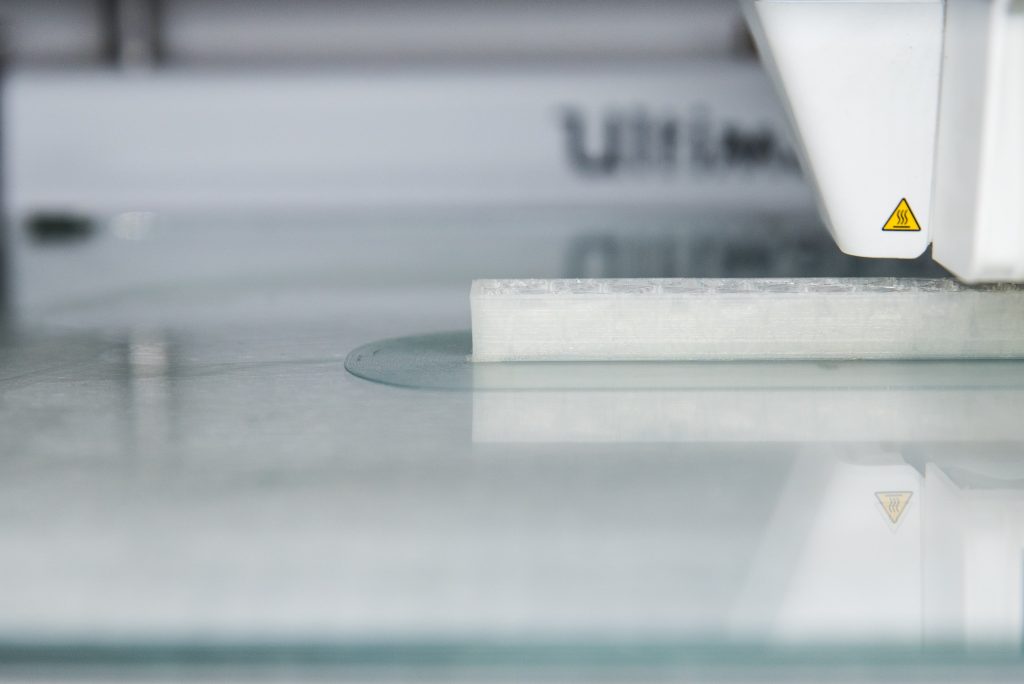
- Use a brim: For the majority of PP prints a 10-20 mm brim is an absolute necessity for a successful print with little to no warp
- Start high then go low: All PP materials benefit from using an additional 10 ˚C for the first layer on both the build-plate and the nozzle. This helps the first layer adhere better but prevents warping and other problems related to excessive printing temperatures.
- Turn off the heated build-plate after the first layer: Some PP materials such as Owen’s corning GF30-PP warp noticeably less when the heated build-plate is disable after the first layer. This helps anchor the material better to the build plate thus arresting warp!
- Print slowly on the first layer: Most materials but especially PP tend to show better first layer adhesion when the first layer is printed slowly (10-20 mm/s)
The right adhesion solution for 3D printing Polypropylene
Unlike home-made or other readily available solutions Magigoo PP was developed to provide optimum adhesion and easy part removal when printing with PP filaments. Magigoo PP has been designed deliver the best 3D printing experience and is easy to use and clean off the build-plate.
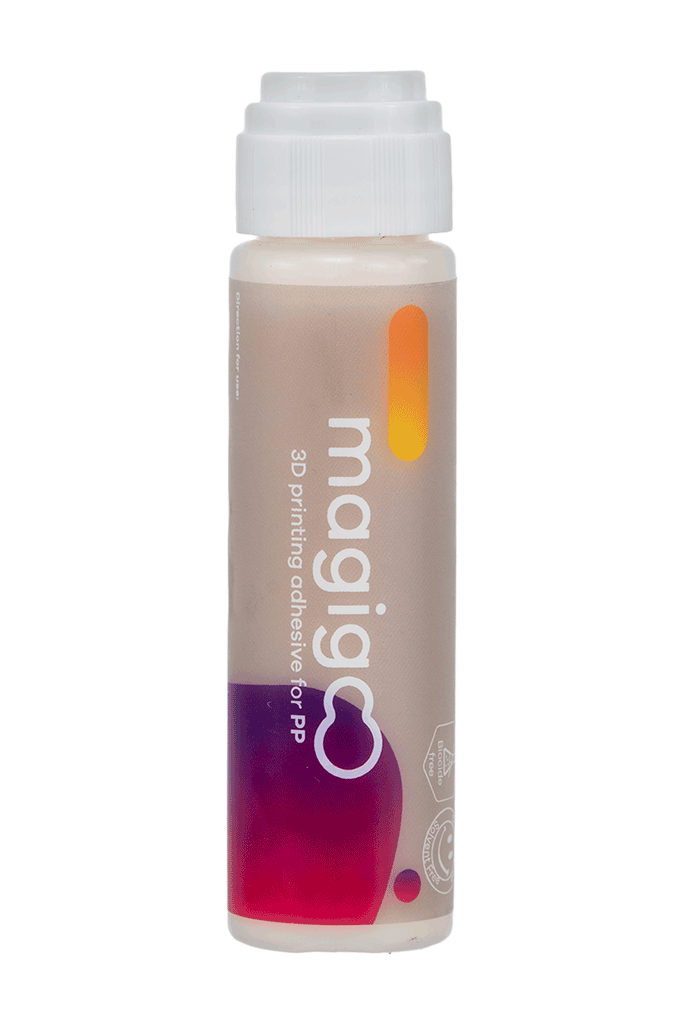
Check out the materials we have tested with our adhesives and stay tuned for more updates in the near future! For more information do not hesitate to contact us on info@magigoo.com!