3D printing – Warping and its causes – Magigoo
Magigoo chemist Jean Paul Formosa, shares his insight and knowlege with regards to 3D print warping. Follow this 4 part blog series to learn about warping and its causes, and how to best reduce it.
In this 4 part series of blog posts we will be exploring :
- Warping and its causes.
- Factors that control the warp.
- Effects of build plate temperature and how better settings result in less warping.
- Improving the first layer adhesion further for perfect 3D prints.
Thermoplastic materials of different material compositions achieve optimum adhesion with different adhesion products. PLA, ABS and PET-G adhere firmly to the Original Magigoo® adhesive when the build-plate is hot and are easy to remove once the build-plate cools down. In addition to the original Magigoo® adhesive which is suited for printing conventional FDM materials, the Magigoo® Pro range consists of four additional adhesives designed specifically for use with different engineering grade materials.
The range includes Magigoo® PC for polycarbonate filaments, Magigoo® PA for Nylon and reinforced Nylon filaments, Magigoo® PP for polypropylene and other poly-olefinic materials and Magigoo® PPGF which is specifically tailored for glass fibre reinforced polypropylene filaments. Magigoo® products (seen in Figure 1) are designed and tested to be used on heated build-plates with glass surfaces, yet Magigoo products also work on other build surfaces such as aluminium, PEI and Kapton tape.
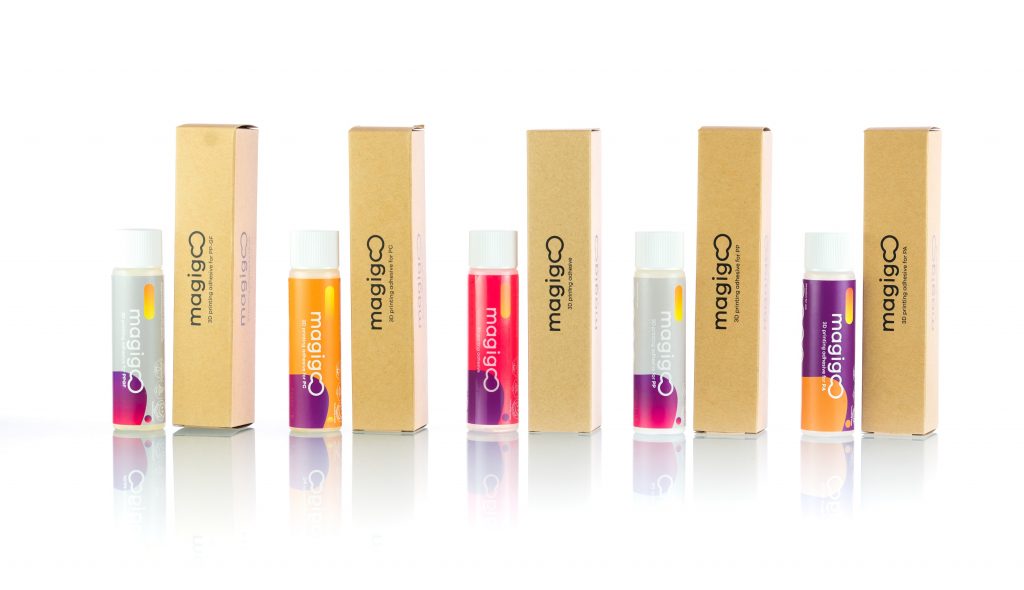
At Magigoo our aim is to help make your bed adhesion issues a thing of the past by suggesting the optimal settings for reliable bed adhesion each time. Unfortunately, every FDM printer and its environment is different so different materials will require different printer settings for optimal adhesion.
Therefore, we have been testing many materials with different Magigoo® adhesives on the Ultimaker S5, so you don’t have to. All the best settings will be shared as a downloadable file at the end of the series. Profiles for these tested materials can also be shared with those interested (kindly send an email to info@magigoo.com requesting these). Kindly scroll down to see this list.
What causes warping?
The FDM printing process requires that a polymer is molten and extruded onto a build-plate or a previous layer of extruded material, layer by layer. Each layer will thus be cooling at different rates leading to a temperature differential when the object is being printed. This manufacturing method will thus result in a part which is cooling non-uniformly, this leads to several issues including warping and print-failure due to insufficient adhesion.
Warping is when the print starts to lift up from the corners and deforming in a lateral direction (Figure 2). In extreme cases warping will cause the print to completely detach from the printer but even in mild cases it can be detrimental due to loss of dimensional accuracy which can lead to the part being unusable depending on the application. The severity of warp will depend on a number of factors with some materials being more prone to warp than others. It goes without saying that for a successful print this detrimental effect needs to be avoided as much as possible.
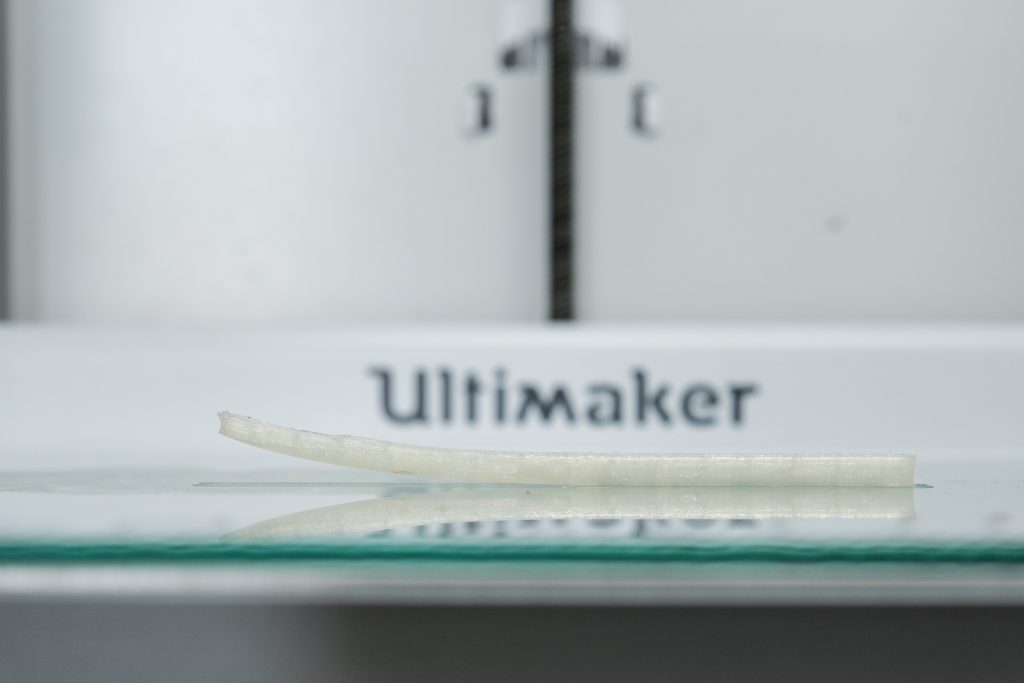
Differential thermal contraction
The cause of warping can be attributed to the differential thermal contraction of each successive printed layer:
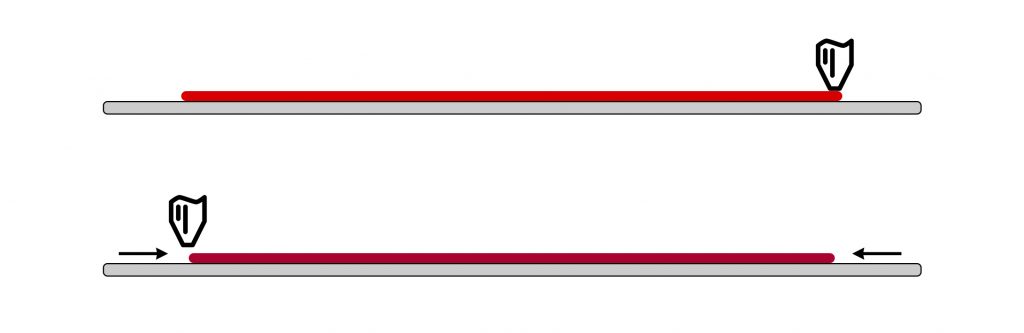
1. When the first layer is extruded onto the build-plate, it starts immediately cooling down to the build plate temperature, this will lead to the first layer to contract slightly (Figure 3).

2. The second layer will be deposited on the already contracted first layer while also cooling down, thus contracting on top of the first layer. Since the bottom layer is already slightly contracted when the upper layer is deposited, the upper layer will cause the layer below it to compress (Figure 4).
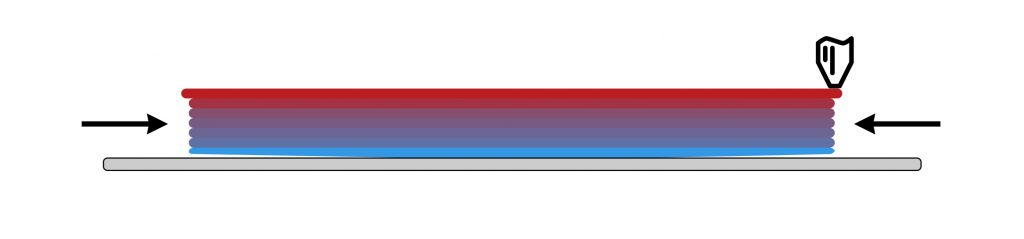
3. This process will keep on repeating itself as new layers are added causing more lateral compression of the lower layers. This results in an overall sheer force between the printed layers which we can call warping stress. If the warping stress is larger than the stiffness of the part and the bed adhesion the bottom of the print will inevitably start pulling away from the build plate. (Figure 5).
Factors affecting warping
Warping is cause due to several factors including the material properties and the printing conditions which are not independent of each other. One of the most important material properties governing the amount of warp in a print is the CTE (coefficient of thermal expansion). The CTE describes the tendency of a material to change its shape, area and volume as the temperature changes. A material with a high numerical value for linear CTE exhibits large changes in length as a response to temperature change. As a result materials which have a high CTE are more prone to warping than materials which do not exhibit large changes in dimensions during the thermal changes present during FDM printing.
In addition to CTE, change in the crystallinity of the material during cooling need to be consider. Crystalline materials such as PP and PEEK will crystallise on cooling from the molten state. Crystallisation can lead to potentially higher shrinkage rates since crystalline structures tend to be more tightly packed. The crystallisation of a material depends on several factors and merits a discussion of its own, at this point it is sufficient to assume that crystalline materials such as PP, some nylons and PEEK tend to warp more than amorphous plastics.
In the next part of this series we will go into further details on how to prevent this warping effect. Make sure not to miss it. In the mean time:
Recommended Magigoo Printing Settings
Manufacturer | Material | Magigoo Type | 1st layer build-plate temperature (°C) | Default Bed Temperature (°C) | Brim (mm) |
BASF Innofil3D | Ultrafuse® PP GF30 | PPGF | 100 | 20 | 20 |
BASF Innofil3D | PP Natural | PP | 80 | 70 | 20 |
BASF Innofil3D | ASA Natural | PC | 110 | 110 | No |
BASF Innofil3D | PET CF | Original | 80 | 75 | No |
BASF Innofil3D | PAHT CF15 | PA | 80 | 75 | No |
Clariant | PA6/66 FR | PA | 90 | 80 | 7 |
Clariant | PA6/66-GF20 FR | PA | 80 | 80 | No |
Colorfabb | XT-Clear | Original | 75 | 75 | No |
DOW® | EVOLV3D™ OBC | PP | 110 | 100 | 20 |
DSM | Arnitel® 2060 HT | Flex | 90 | 80 | 20 |
DSM | Novamid® 1030CF | PA | 70 | 65 | No |
DSM | Novamid® 1070 | PA | 95 | 85 | 20 |
DSM | Arnitel® 2045 | Flex | 80 | 70 | 20 |
DSM | Novamid® 1030 | PA | 80 | 80 | 7 |
DuPont™ | Zytel® 3D1000FL | PA | 100 | 90 | 20 |
DuPont™ | Hytrel® 3D4100FL | PA | 105 | 95 | 20 |
Fibreforce | Nylforce CF | PA | 90 | 85 | 20 |
Fibreforce | Nylforce GF | PA | 100 | 90 | 20 |
Filkemp | Nylon | PA | 70 | 70 | No |
FormFutura® | Centaur PP | PP | 80 | 70 | 20 |
Fiber Three | F3 PA Pure Lite | PA | 80 | 80 | No |
Fiber Three | F3 PA Pure Pro | PA | 80 | 80 | No |
IGUS® | Iglidur I180 | PC | 110 | 110 | 20 |
Lehmann Voss | LUVOCOM® 3F PAHT CF 9742 BK | PA | 105 | 100 | No |
Lehmann Voss | PAHT | PA | 70 | 70 | No |
Lehmann Voss | LUVOCOM® 3F PAHT GK 9874 NT | PA | 70 | 70 | No |
Matterhackers | Nylon X | PA | 90 | 80 | 8 |
Matterhackers | Nylon Pro | PA | 70 | 70 | 7 |
Matterhackers | Nylon G | PA | 90 | 80 | 8 |
Owens Corning | X-Strand™ GF30-PP | PPGF | 100 | 20 | 20 |
Owens Corning | X-Strand™ GF30-PA6 | PA | 75 | 70 | No |
Polymaker | PolyLite™ PC | PC | 110 | 110 | No |
Polymaker | PolyMide™ PA6-GF | PA | 75 | 75 | |
Polymaker | PolyMax™ PC | PC | 110 | 110 | No |
Polymaker | PolyMide™ PA6-CF | PA | 75 | 70 | No |
Polymaker | PolyMide™ CoPA | PA | 70 | 70 | No |
Taulman3D | Bridge | PA | 70 | 60 | 20 |
Taulman3D | 645 | PA | 70 | 60 | 20 |
Taulman3D | 680 | PA | 70 | 60 | No |
Ultimaker | CPE | Original | 75 | 75 | 7 |
Ultimaker | TPU95A | Original | 0 | 0 | 8.75 |
Ultimaker | PC | PC | 105 | 105 | No |
Ultimaker | Nylon | PA | 90 | 80 | No |
Ultimaker | PP | PP | 80 | 70 | 20 |
Ultimaker | ABS | Original | 85 | 85 | 7 |
Verbatim | PP | PPGF | 80 | 70 | 20 |