3D Printing Composite Materials
The FDM 3D printing of composite material filaments opens up novel possibilities for 3D printed parts. A variety of different filler materials can drastically alter the properties of thermoplastic materials and the resulting printed parts. The appearance, mechanical properties, electrical properties or thermal properties of a material will thus also depend on the filler particles used and not just the base material.
Introduction – What are composite materials?
As their name suggests, composite materials are materials which have a composition of two or more materials. A carrier material or a matrix, which in the case of 3D printing filament is a thermoplastic material such as PLA, ABS or Nylon, and a filler material, which is insoluble in the matrix material. The filler material thus forms distinct and separate regions within the matrix material and will thus impart characteristics to the material which are different from that of the individual component. The properties of the resulting composite will depend on several factors, including the type of filler material present, its amount and also the shape and size of the filler particles and how well they interact with the matrix material. The matrix material will also influence the characteristics of the resulting material. In the case of FDM thermoplastic composites, the final material must retain thermoplastic behavior to enable fabrication of the composite.
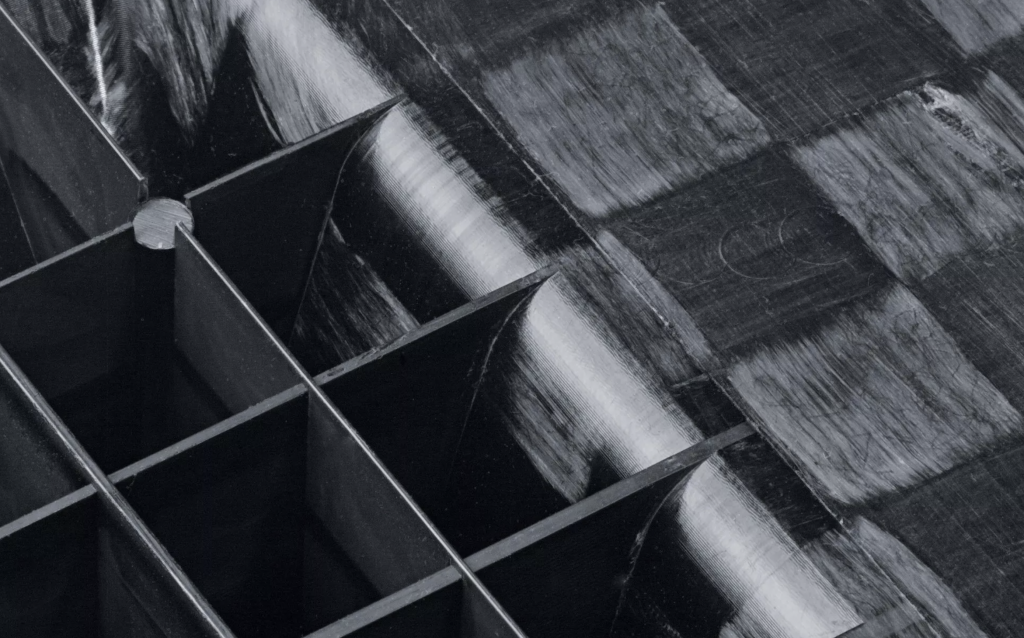
Why Composites?
As mentioned previously there are several reasons for 3D printing composite materials. In some cases the choice might be due to aesthetic reasons however filler materials can also impart additional functionality and improve the mechanical properties of a thermoplastic material.
Appearance
The filler material in a composite filament will impart different visual characteristics to a filament. For example wood particles will make the printed part look similar to a wooden part while copper filled filament will make the part look more like copper. Generally unlike their neat counterparts, composite filaments tend to produce prints with a grainy texture. This imparts a very different finish to the printed part and helps hide the layer lines quite well. On the downside, filament filled purely for aesthetic reasons tend to show inferior durability than the unfilled material (usually PLA) since the filler material makes printed parts more brittle.
There are a variety of composite materials in this category including:
Wood Filament
Wood filament is probably one of the more popular 3D printing composite filament types. With this filament it is fairly easy to obtain good quality prints. furthermore, the layer lines brought about by the FDM process will mimic the appearance of natural wood grains.
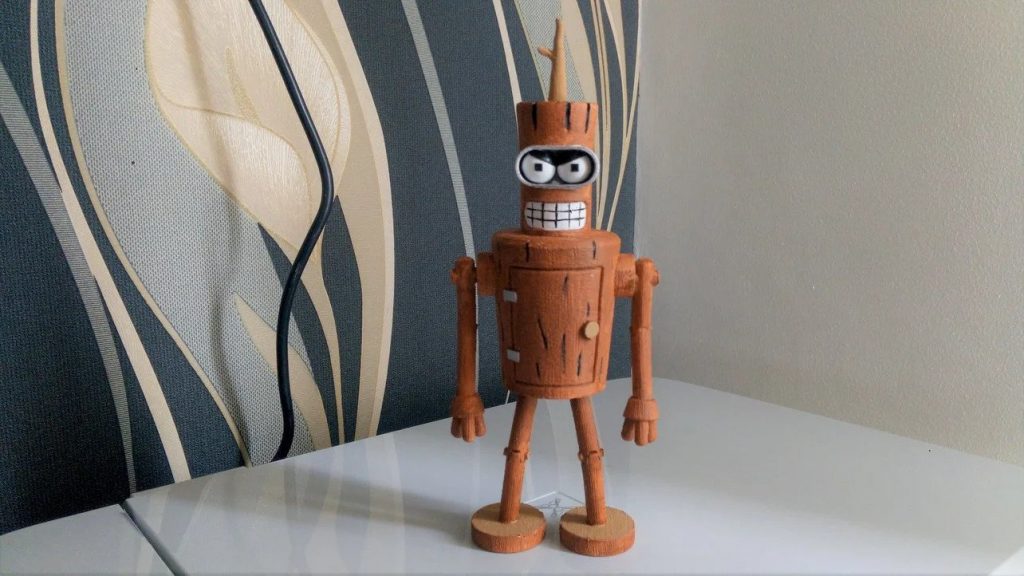
Wood filaments can have different filler materials embedded in them including wood dust, bamboo or cork. Each type of filler material will give the printed part a different look, but the physical properties are more or less the same. Parts printed in wood filament can also be sanded easily and stained and varnished just like regular wood. This makes it very easy to produce parts which mimic wood very closely using 3D printing!
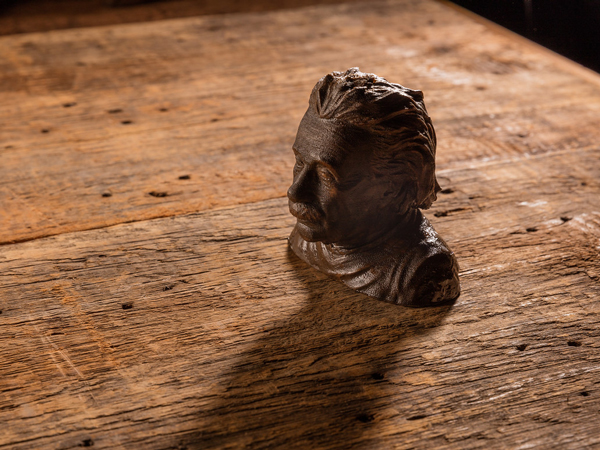
Metal Filament
In the FDM sphere Metal composite filament generally refers to PLA filaments impregnated with metal powders. Metal filament can be used to create printed parts with a similar look and feel to metal parts. Typically, metal filaments are filled with copper, brass, stainless steel or aluminum and usually have a higher amount of filler material, with values of around 80% wt.
The high filler ratio means that the filament typically has a very high density and will also make the material more thermally conductive. As a result, printed parts will have a solid weighted feel when compared to parts printed in regular PLA. The increased thermal conductivity also means that lower printing temperatures are required to print these materials. The added heft however does mean that bridges and overhangs are harder to print than with regular PLA.
Once printed, the parts can be sanded and polished to a give a metallic shine to the finished part. Furthermore, some metal filaments can also be processed by ‘oxidising’ the parts to simulate the look of corroded or rusted metal.
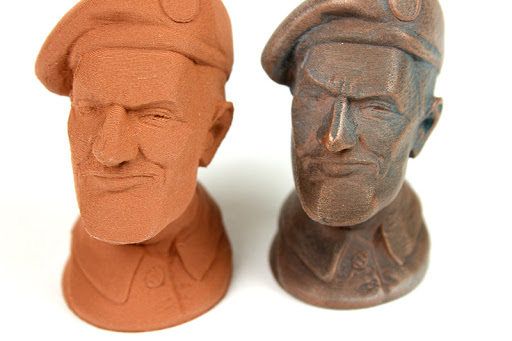
Stone Filament
Another class of composite filament is stone filament which is composed of fine chalk particles in a PLA matrix. This gives the filament an appearance similar to that of stone. Furthermore, stone filled filaments typically come out printed with a gritty texture which dramatically reduces the appearance of layer lines. Similarly to metal filaments stone filaments produce parts which are typically heavy and thus runs into similar printing issues as metal filaments.
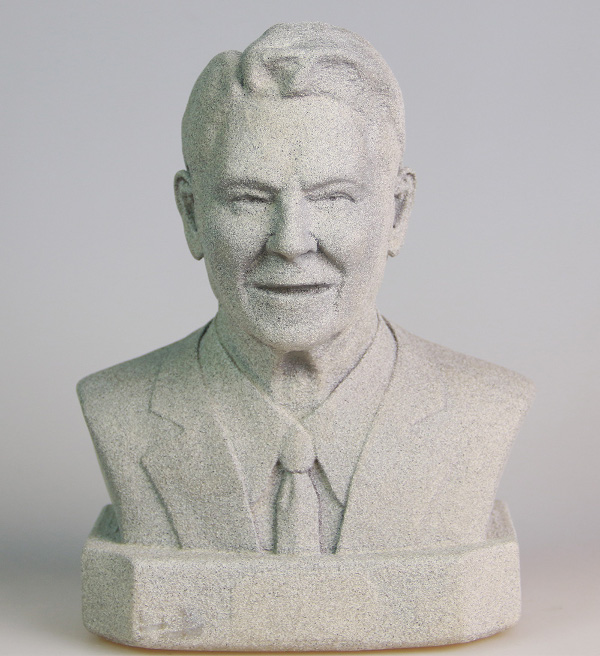
Filaments can also be filled with finely powdered marble particles. This gives the printed parts a speckled finish due to the presence of dark and light particles in the filament. As a result the printed parts do not look like parts carved out of marble. Nonetheless the speckled appearance gives a pleasing finish which also hides the layer lines in prints very well.
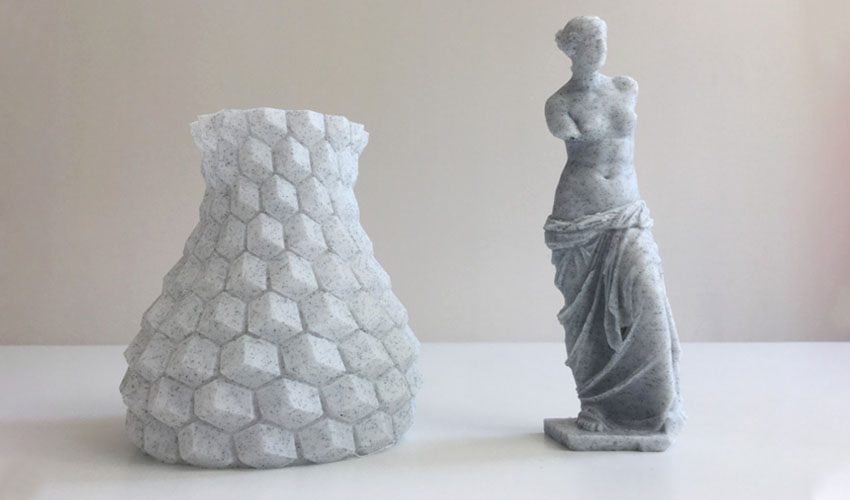
Glow in the dark Filament
As the name suggests glow in the dark filament produces parts which glow in the dark after exposure to light. This is a similar effect to glow in the dark toys which absorb light from the environment and emit it slowly when the environment is sufficiently dark.
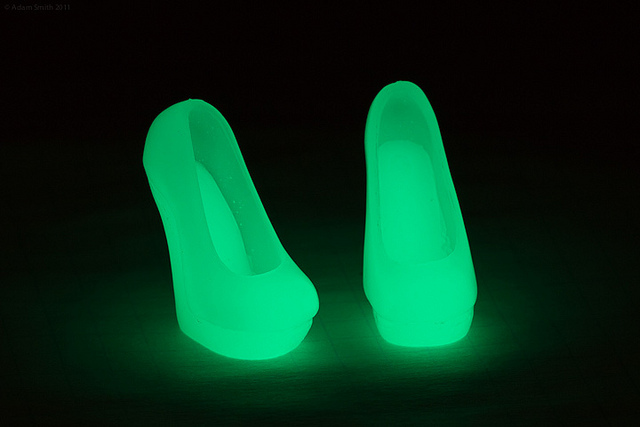
Glow in the dark filaments are typically made of ABS or PLA embedded with strontium aluminate, a phosphorescent compound. Typically parts having thicker walls and a higher infill ratio will sow a brighter glow due to the additional material in the print.
Functionality
Conductive Filament
While one might think that metal filament might be conductive, due to the insulating properties of the PLA matrix, current cannot pass through part printed in metal filament. Not sufficiently at least. In fact conductive filament is filled with graphene which enables the movement of electrons in plastic parts.
Nonetheless conductive filament still does not conduct metal nearly as well as metals do. In fact conductive filament is typically used to create custom electromagnetic and radiofrequency shields.
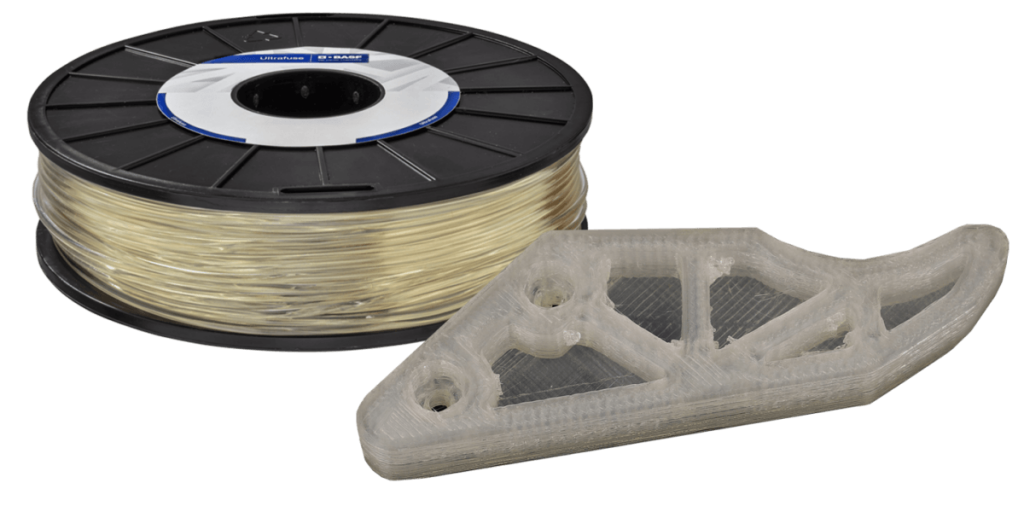
Another class of materials is labelled as ESD (Electrostatic Discharge) safe. These materials are conductive enough to prevent the buildup of electrostatic charges which might damage sensitive electric components. Conductive and ESD safe filaments are typically more expensive due to the high cost of graphene.
Magnetic Filament
Similarly to metal filaments magnetic filaments are filled with metal particles. However in this case the particle are ferromagnetic. Typically iron powder is used which produces hefty parts which are attracted to magnets. In fact magnetic filaments do not produce parts which are inherently magnetic but parts which can be attracted to a magnet. Since the filler material is iron, the printed parts can be sanded and exposed to saline water to produce a rusty finish.

Metal Filament
Some types of metal filaments can also be functional in the sense that they can be used to produce fully metallic parts on a regular FDM printer. These filaments contain a high percentage of metal filler in a special polymer matrix that makes this process possible. An example of such filament is BASF Ultrafuse 316L which we have discussed in a previous article. The printed part will then go through a bespoke process which first removes the polymer matrix to leave a solid part of metal particles which are then fused through a sintering process.
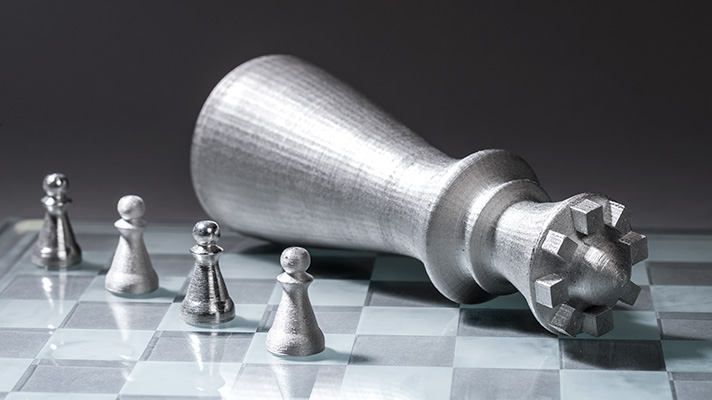
Other metal filaments which can be treated to form solid metal parts are available as well.
Mechanical Properties
A very interesting application of composite materials in FDM printing is the use of filler materials. Filler materials, generally in the form of fibers are added to enhance the mechanical properties of thermoplastic materials. Filled thermoplastics can exhibit exceptional improvement in the mechanical strength and stiffness of a material when compared to a similar unfilled material.
Typically; glass, carbon or Kevlar fibers are added to engineering thermoplastics such as Nylon, Polycarbonate, Polypropylene, ABS and PEEK giving rise to a multitude of possibilities when it comes to the production of functional parts produced by FDM printing. These fibers typically have a very high strength under tension, thus the incorporation of these materials within the polymer will reinforce the material under tensile load. When aligned to the direction to which force is applied, the polymer matrix will transfer the applied load to these fibers which will resist deformation. As a result, the shape, type, orientation, and relative amount of the reinforcing fibers will influence the reinforcing effects on the material.
The addition of filler materials also improves the dimensional and thermal stability of a polymer. As a result there is a growing demand for use of these materials for the production of FDM parts to be used in the automotive and aerospace industry
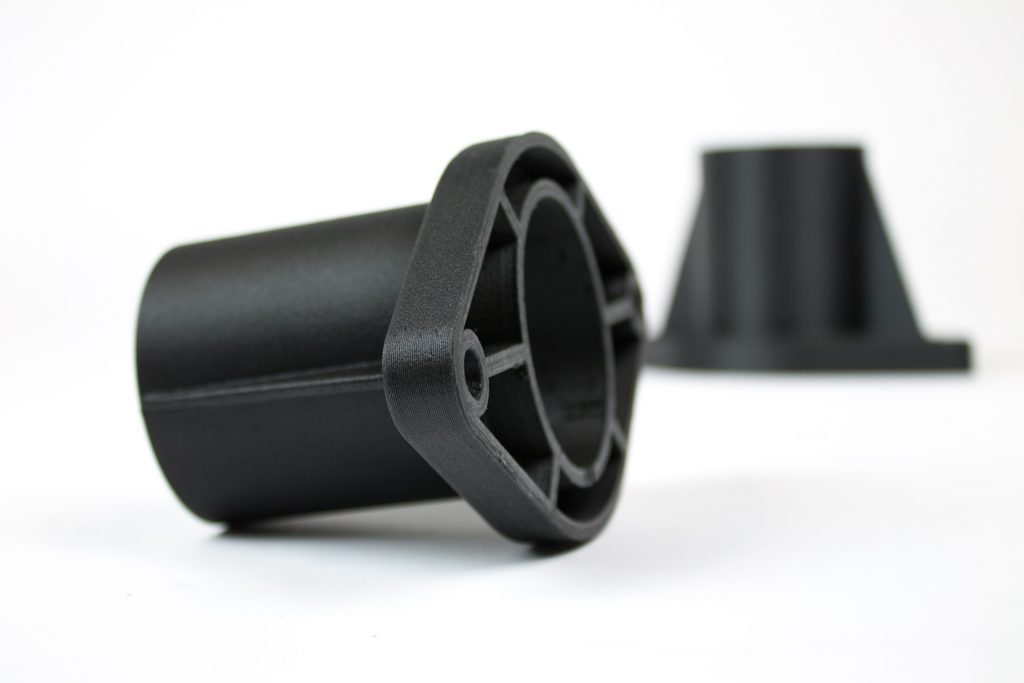
The table below shows two materials from fiberthree. One is an unfilled Nylon (F3 PA Pure Pro) and the other is filled with 15% carbon fibers (F3 PA-CF Pro). It is immediately obvious that the filled material is much stiffer and stronger than the unfilled nylon, while the density of both materials is quite similar. The filled material also shows superior temperature resistance albeit with decreased ductility as suggested by the lower elongation values.
F3 PA Pure Pro | F3 PA-CF Pro | |
Density (g/cm³) | 1.2 | 1.25 |
Tensile Modulus (MPa) | 3400 | 14400 |
Tensile strength (x-y) (0°) (MPa) | 80 | 120 |
Elongation (0°) (%) | 3.65 | 0.98 |
Heat Distortion Temp (°C) | 90 | 120 |
Another way to improve the mechanical strength of printed parts is to embed continuous fibers during the printing process. The technology is used by a number of printer manufacturers including Markforged, Desktop Metal and Anisoprint. This results in parts with exceptional strength and stiffness rivalling those of metal along the direction of the laid carbon fibers. However these types of AM manufacturing processes differ slightly from the regular FDM process and warrant an article on their own!
3D printing Composite Materials
Composite materials usually do not require more expertise to print than the base material. In fact, in some cases, composite materials can be easier to print since the addition of filler material increases dimensional stability and reduces warping. The addition of hard filler material particles however does also mean that there will be more wear on printer components moving and extruding the filament. This includes the extruder gears which should preferably be swapped out for hardened materials if you are printing a lot of composite filaments.
More importantly the nozzle will also experience much higher levels of wear when printing composite materials. It is recommended to switch to a hardened steel nozzle when printing any type of composite filament. since brass nozzles will wear out very quickly. Additionally, one can also switch to a ruby nozzle which should last much longer than hardened steel nozzles.
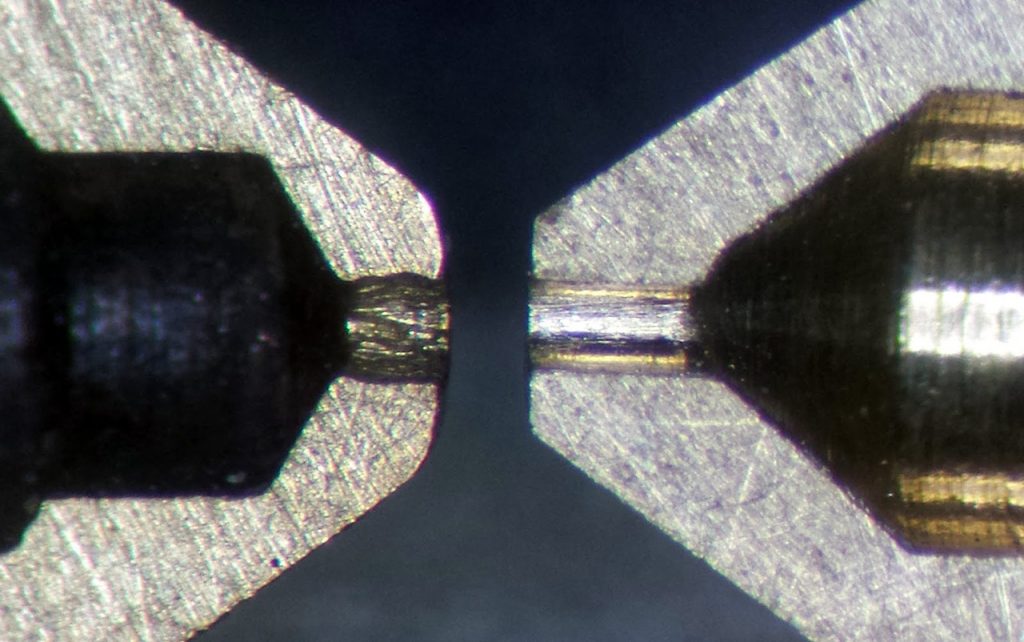
Another consideration when printing with composite materials is the nozzle diameter. Since composite materials are filed with particles these tend to clog smaller diameter sized nozzles which will lead to under-extrusion and also failed prints. In most cases it is recommended to use a nozzle diameter of at least 0.5 mm to avoid nozzle clogs with composite filament.
Build-plate adhesion
As previously stated in most cases composite filaments tend to warp less due to the extra dimensional stability brought about filler particles. As a result for most materials, the build-plate adhesive which is usually used with the neat material will also work well for the filled material. Nonetheless in some cases adhesion might still be challenging with some types of composite materials such as GF-30PP and BASF Ultrafuse 316L. Both these materials prove to be quite challenging to print and thus a bespoke adhesive solution has been developed for both these materials.
We hope that you have found this blog series on different classes of 3D printing materials interesting. Other articles include:
3D Printing Polycarbonate – Why and how?
3D Printing Polypropylene – Why and how?
3D Printing with Nylon – Why & How?
3D Printing Flexible Materials – A short guide
3D Printing High Temperature Materials
Ultrafuse 316L – Printing metal on your desktop printer
Have any feedback or suggestions for us? let us know on info@magigoo.com