Choosing the right 3D printing materials for FDM – Opinion
This article is an opinion piece from our Magigoo wizard where he discusses the use of common 3D printing materials, their strengths and weaknesses!
Thermoplastic materials – an introduction
Polymers are made of large molecules with a repeating chemical structure, otherwise known as a monomer. The mechanical and chemical properties of a polymer are affected not only by the chemical make-up of the repeat unit but also the molecular arrangement of the repeat units in the polymer chains, and, the interactions between these polymer chains. In thermoplastic materials, the polymer chains are held together with weak intermolecular forces. As a result, thermoplastic materials can be repeatedly softened from a solid to a viscous fluid on application of heat.
Currently most of the thermoplastic material types available for injection moulding are also available for 3D printing, with more materials being adapted for FDM AM each day. Figure 1 below shows the common material classes available for 3D printing. The materials are split into three different classes; commodity, engineering and high temperature, with some materials overlapping the commodity and engineering class.
Generally, engineering materials tend to require higher nozzle and chamber temperatures than commodity plastics during printing, since these materials tend to have higher melting temperatures. Printing at lower than recommended temperatures will potentially lead to print failure or parts with inferior mechanical properties. Similarly, high temperature thermoplastics require even higher nozzle and working temperatures for printing. These materials often require an actively heated build chamber during printing for reliable results.
FDM printing and its pitfalls
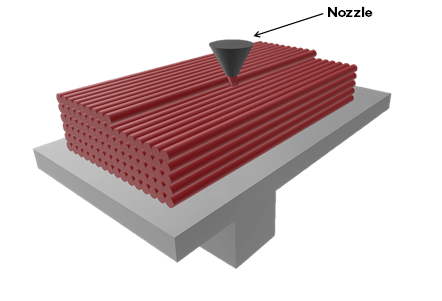
Due to the layer upon layer nature of FDM parts (figure 2) tend to have voids or empty spaces between the layers which are detrimental to the mechanical properties of the final part. As a result, the bond strength between layers of extruded material is often cited as being the weakest and most critical parameter affecting the mechanical properties of FDM parts. In other words, 3D printed parts are often much weaker in the Z-direction than in the X- and Y- direction.
The adhesion between printed layers is achieved through thermally-driven diffusion welding. Thus, different fabrication parameters including nozzle temperature, environmental temperature, print speed, nozzle width, extrusion width, layer height and others will have an effect on the resulting mechanical properties of a printed object. Since different materials have different temperature requirements, the material type will also affect the z-strength of a printed part. In fact higher temperature materials are more prone to poor z-strength and delamination if the printing parameters are not adequate.
Common 3D printing materials – are they good enough?
One of the misconceptions I’ve held when I started working in the 3D printing sphere was that PLA is only suited for aesthetic prints and that functional prints using PLA were not feasible. This is due to the fact that often parts printed with PLA tend to break easily especially in areas with thin sections. This would lead one to believe that PLA is not a very strong material. However when looking at the typical mechanical properties for this material in the table below, one can easily see that it is stronger than most common ‘engineering’ materials in terms of Ultimate tensile strength and also in terms of stiffness. CNCkitchen also did some interesting tests with these materials.
PLA | PET-G | ABS | Tough PLA | |
Nozzle (°C) | 205 | 240 | 255 | 210 |
Bed (°C) | 60 | 80 | 100 | 60 |
Tg (°C) | 61 | 81 | 101 | 60 |
Strength (XY – MPa) | 46.6 | 31.9 | 33.3 | 41 |
Strength (Z – MPa) | 43.5 | 13.4 | 25.4 | 33 |
Stiffness (XY – MPa) | 2636 | 1472 | 2174 | 2450 |
Stiffness (Z – MPa) | / | 1087 | 1835 | 2200 |
Ductility (XY – %) | 1.90 | 6.8 | 2.7 | 20 |
Ductility (Z – %) | / | 1.3 | 2.4 | 2.6 |
Impact Strength (XY – kj/m2) | 2.68 | 5.1 | 12.6 | 22.9 |
Impact Strength (Z – kj/m2) | / | / | 10.5 | 2.2 |
Typical mechanical properties of common 3D printing materials
So why does PLA break so easily?
In my opinion this is a result of a combination of factors including:
- PLA has very low ductility and is thus very brittle. In laymans terms, this means that PLA does not like to bend and tends to snap like glass
- The inherent inferior mechanical properties in the z-direction as discussed above – especially when using low nozzle temperatures and active part cooling. This usually results in prints with a smoother finish and less artefacts at the cost of Z-strength
- Design which does not take into consideration of these factors. While some designers take into account the material and manufacturing limitations, others don’t. The relative ease by which even inexperienced users, (such as myself starting out) can design and print parts means that in most cases these design requirements are overlooked.
As a result when all these factors are combined, the resulting printed parts will be fragile and unsuited for functional applications. Nonetheless with a good design approach and by slightly tweaking printing and slicing settings, one can get very strong parts out of PLA which will endure years of hard use, PLA also has the advantage of being easy to finish, paint and is also relatively easy to machine.
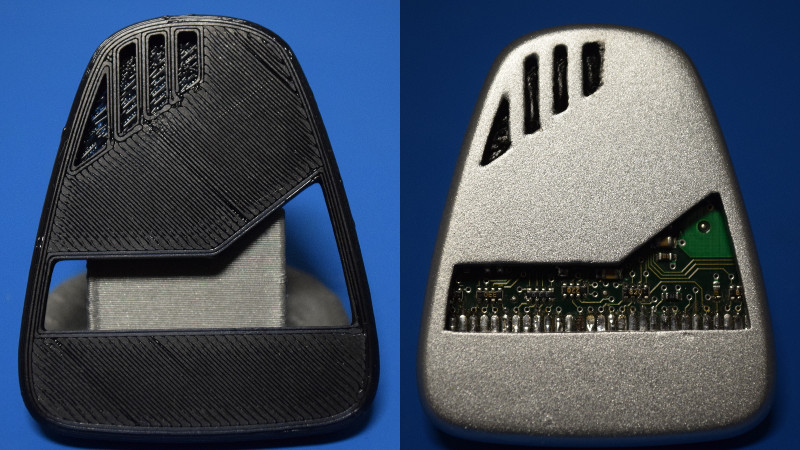
With that being said PLA still has its limitations especially in applications which require repeated loadings and also large extents of flexure and plastic deformation during use. The major drawback of PLA is however its relatively low temperature resistance. PLA has its glass transition at around 60 °C or lower. This means that at extreme ambient temperatures, such as in a hot car during summer, the material can easily become soft enough to deform, even under light or no stress. This limits the practical applications of PLA somewhat.
How about ABS?
ABS is generally regarded as being more suitable for general use plastics and everyday commodity materials. This is due to the fact that ABS is a copolymer, more accurately a terpolymer of Acrylonitile, Butdiene and Styrene. Without going into too much detail, the mixture of these three monomers give ABS respectable toughness and impact resistance and an operating temperature of between -20 °C to 80 °C which suits the typical usage scenarios of most everyday items. Coupled with its relatively cheap price, and ease of production and post processing ABS quite frequently used as a thermoplastic.
More importantly ABS was probably the most common material that was widely available for FDM printing during its early years leading to its popularity in 3D printing. Nowadays while still widely used, and still a go-to material for 3D printing, it faces stiff competition from other materials such as ASA and PET-G in generic cases and other engineering materials in more specific applications.
Apart from it’s versatile material properties ABS has several advantages when it comes to 3D printing. These include the aforementioned ductility which means that parts are less much less prone to brittle, unpredictable failure and the material’s higher temperature resistance when compared to PLA. ABS is also one of the cheapest and most readily available 3D printing filaments. Furthermore ABS is soluble in acetone, as a result parts can be ‘glued’ together using acetone and also vapor smoothed to remove the appearance of layer lines.
ABS also has several disadvantages when it comes to 3D printing. These include the material’s tendency to warp, however this issue has been long solved with the use of build-plate adhesives such as Magigoo Original. Since the material has a higher temperature requirement it is also recommended that an enclosed or actively heated printer is used with this material for printing larger parts. Otherwise there is a greater chance for the resulting prints to exhibit delamination and inferior mechanical properties in the Z-direction. As a result there is a greater chance that parts printed in this material break easily if the environmental temperatures are not accounted for. ABS is also known for its characteristic smell when printing. In fact ABS releases toxic fumes when heated and it is recommended to print this material in a well ventilated area.
ASA
ASA (Acrylonitrile Styrene Acrylate) is a material which is quite similar to ABS in terms of mechanical and thermal properties. In fact in most cases ASA can be printed using similar temperature settings and printing conditions to those used for ABS. The advantages of ASA is its vastly superior resistance to UV rays and water and chemicals resistance. This makes the material better suited for external parts.
PET-G
PET-G (Polyethylene Terephthalate – glycol modified) is another popular 3D printing material that can be considered as the middle ground between ABS and PLA. While still being relatively easy to print, with a glass transition temperature of around 80 °C, PET-G offers better temperature resistance than PLA. This material is also softer and less stiff than both PLA and ABS, this reduces the machinability of the material, but allows for greater ductility. In fact PET-G is the one of the most ductile materials which can be easily printed. This makes it especially useful for parts which have to withstand large deformations and makes printed parts very hard to destroy.
Nevertheless in terms of mechanical strength and stiffness PET-G is the generally the weakest of the bunch and is thus less suited for parts which need to bear higher static loads.

Tough PLA
Another alternative material which is still easy to print and quite popular is tough PLA. This material combines the stiffness of PLA with the toughness of ABS whilst retaining excellent layer adhesion. In fact this material is ideal for application requiring high toughness and rigidity. It is still easy to print yet it is much less brittle than PLA and thus less prone to unpredictable failure. The downside is that this material has similar thermal resistance as PLA and thus is not suited for high temperature applications.
Engineering and High Temperature 3D printing materials
If however the aforementioned materials don’t cut it in terms of mechanical, thermal and chemical properties there is a vast selection of other FDM materials available. Apart from offering improved mechanical properties Engineering materials often excel at particular applications. Several classes of engineering materials have already been discussed in previous articles, these include:
Polypropylene (PP)
PP is a very useful material and is one of the most commonly used thermoplastics in injection moulding due to its low cost and flexibility. PP exhibits high toughness, flexibility, fatigue resistance and excellent chemical resistance. Some grades of PP are also surprisingly heat resistant and resistant to attack by acids, water, detergents, oils and fats. Furthermore PP can be used in food safe applications due to its relative inertness.
PP thus finds its way in a variety of products including food packaging, food containers, utensils, athletic apparel and automotive parts such as car batteries. PP utensils can also be autoclaved and thus PP also finds use in laboratory and surgical equipment. Due to its fatigue resistance polypropylene is often used for the creation of living hinges.
Nylon
Nylon is a thermoplastic material that comes in a variety of flavors and is very versatile. Nylon can show exceptional strength, durability, elasticity, chemical resistance and even thermal resistance. Nylon also has a very low surface friction which makes its highly resistant to wear. As a result, nylon finds itself being used in a variety of applications. These include plastic gears, low and medium load mechanical parts, bushings and bearings. Nylon is also used for a variety of injection molded parts for vehicles, electrical equipment and mechanical equipment.
Polycarbonate (PC)
Polycarbonate exhibits superior temperature resistance (up to around 135 ˚C) and impact resistance making it useful as an engineering plastic. PC can also undergo large plastic deformation prior to cracking. The strength, toughness, optical clarity and ease of fabrication of PC lends to a variety of uses including kitchen appliances, lenses, windows and is also used to make CDs. Polycarbonate can also contain flame retardant additives and is an inherently electrically insulating material. Thus it finds itself being routinely used in electrical and automotive applications.
Flexible Materials
As their name suggest flexible material are materials which are easily deformable and have a degree of elasticity. Flexible materials come in a number of varieties, from soft materials which can be easily deformed before returning to their original shape, to firm materials which only flex slightly under load. The ease of deformation of material depends on the stiffness of the material and is often indicated by the hardness value.
Composites
Composite materials consist of a composition of two or more materials. A carrier material or a matrix, in this case a thermoplastic material such as PLA, ABS or Nylon, and a filler material, which is insoluble in the matrix material. Filled thermoplastics can exhibit exceptional improvement in the mechanical strength and stiffness of a material when compared to a similar unfilled material.
Typically; glass, carbon or Kevlar fibers are added to engineering thermoplastics such as Nylon, Polycarbonate, Polypropylene, ABS and PEEK giving rise to a multitude of possibilities when it comes to the production of functional parts produced by FDM printing. The addition of filler materials also improves the dimensional and thermal stability of a polymer. Thus, there is a growing demand for use of these materials for the production of FDM parts to be used in the automotive and aerospace industry
High Temperature Materials
When it comes to FDM 3D printing, successfully printing with high temperature materials is still one of the most demanding prospects. These materials require printing temperatures which are often markedly higher than those of regular FDM materials. High temperature materials often have exceptional thermo-mechanical and chemical properties and are usually reserved for high end applications in the aerospace, automotive, healthcare, research and manufacturing industries. These materials often retain their stiffness at elevated temperatures where commodity and engineering plastics such as ABS and Nylon tend to become soft and pliable. There are currently a number of high temperature thermoplastic materials available for FDM 3D printing, these include: PEEK, PEKK, ULTEM 1010, ULTEM 9085, PPSU, PPSF and PVDF
It is not just the Material!
As previously mentioned when discussing PLA, sometimes 3D printed parts can fail sooner than expected. Apart from the inherent limitations brought by the layer by layer build several factors affect the final strength of the printed part. However with some design and process considerations premature part failure can be mitigated. Given that the correct material is chosen for the application depending on the intended use of the end part one also needs to look out for:
Part orientation and design
This is probably the most important consideration when it comes to using the FDM process to produce objects. On one side it is generally preferred to minimize the use of support structures when printing. the use of support structures increases printing time and material usage but more importantly adds an extra post-processing step for support removal. Nonetheless if part integrity is the main requirement, the part must be oriented in such a way as to avoid it being loaded perpendicularly to the build-direction during use.
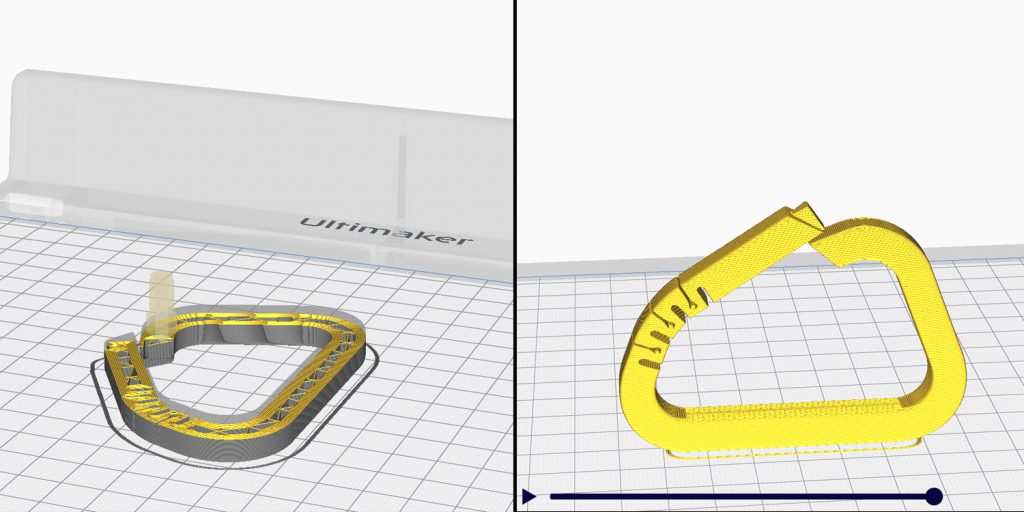
As previously mentioned, another factor which needs to be considered is the design of the part. This article from 3D hubs covers a few of the basics however the design consideration will be highly related to the function of the part. This would require more in depth knowledge of design in relation to static and dynamic forces.
3D printing settings
Once you have chosen the correct material it is also important to find out the correct settings for your printing set-up. The nozzle, build-plate and chamber temperatures, part cooling and print speed will all affect the resulting mechanical properties of the final part, especially in the z-direction. It is thus important to optimize the settings for layer adhesion, there are several articles online on how this can be achieved by calibrating these temperatures. One must also consider if the printing set-up being used is capable of printing the required material at the optimal settings. While some open printers can reach the temperatures required to print polycarbonate for example, this does not mean that large polycarbonate parts can be printed on these types of printers without an appreciable loss in layer adhesion!
Other factors such as extrusion width, layer height, nozzle size, number of shells and infill density also affect the strength of the printed parts.
Model issues
Another point which is worth mentioning are issues with STL files leading to 3D printing artefacts. These include non-manifold edges, holes and gaps, unmerged bodies and hollow structures. It is thus always a good idea to preview the g-code thoroughly before printing an to look for these errors. This happens more often than you’d think and can leave you wondering why a part is failing, only to find out that it was a problem with the virtual model on the machine.
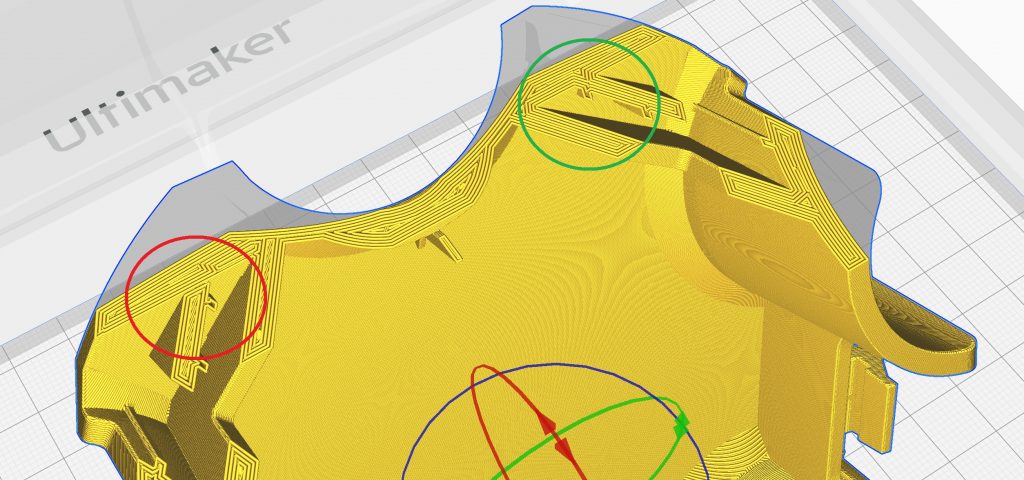
Looking at the figure above it can be seen that in the case of the part circles in red, one of the clips on the print is being treated as a separate body, even though this was not immediately apparent in the .stl file. On the other hand the same clip on the other side (encircled in green) is treated as a part of the whole body. It can be immediately observed that in the first case the printing paths for the clip do not incorporate it into the body which means that the clip will fail under much lighter loads than the clip marked in green.
I hope you found this blog article informative! Watch out for our next blog article which will feature some useful 3D printed camera accessories!